3D-gedruckte Erdbebensicherheit
Erstes erdbebensicheres 3D-gedrucktes Gebäude in Italien
Zum ersten Mal in Italien wurde in einem Erdbebengebiet ein Gebäude 3D-gedruckt. Heidelberg Materials stellte Enel Green Power und der Universität Neapel Federico II ein innovatives zementartiges Material zur Verfügung, um für einen Teil der elektrischen Ausrüstung ein kleines Industriegebäude und ein Fundament zu drucken.
Die Konstruktion wird Teil eines Umspannwerks in der BESS-Anlage (Battery Energy Storage System) im Kraftwerk Alessandro Volta in Montalto di Castro (Latium, Mittelitalien) sein. Die entwickelten Prototypen können einen wichtigen Durchbruch darstellen: Die 3D-Druck-Technologie verkürzt die Bauzeiten und macht das Bauen nachhaltiger.
Zu ihren Vorteilen gehören ihre Anpassungsfähigkeit an spezifische Bedürfnisse und ihre optimierte Bauleistung.
Dank des hohen Digitalisierungsgrades macht der 3D-Betondruck Baustellen sicherer und ermöglicht Bauwerke mit komplexen Formen und maßgeschneiderten Details, die mit herkömmlichen Methoden nur schwer oder gar nicht zu realisieren wären,
bestätigt die Ingenieurin Martina Palomba, die in den Forschungs- und Entwicklungslabors von Heidelberg Materials arbeitet.
Alle Strukturelemente wurde im Industriegebiet von Volla (Neapel) hergestellt: Hier wurden dank der Zusammenarbeit mit der Universität Neapel Federico II und ihrem Spin-off Etesias die beiden Fundamente und Wände geschaffen und dann in Montalto in Teamarbeit wie ein riesiges Lego-Set zusammengebaut. Ein Roboterarm druckte jedes Bauteil, indem er ein Endlosfilament aus 3D-druckbarem Material auftrug. Dieses mehrere Kilometer lange Filament folgte einem vorgefertigten Pfad. Dazu reproduzierte eine spezielle Software das digitale 3D-Modell. Der verwendete 3D-druckbare Mörtel ist das zementartige Material i.tech 3D von Heidelberg Materials (die Marke, die vormals in Italien unter Italcementi firmierte). Der Prozess ist fast vollständig automatisiert, und das Technik-Team muss lediglich die Qualität des gemischten und gepumpten Materials überprüfen und die Druckparameter wie die Extrusionsgeschwindigkeit des Filaments oder die Geometrie jedes Blocks kontrollieren.
Die Vorteile der 3D-Konstruktion: Schnellere Baustellen, geringere Kosten und weniger CO₂
Obwohl 3D-druckbares Material derzeit teurer ist als herkömmlicher Beton, ist der Bauprozess viel schneller und bequemer: Wir sprechen von einer Zeitersparnis von mindestens 50 %. Auf dem Energiemarkt, insbesondere im Bereich der erneuerbaren Energien, bedeutet Schnelligkeit mehr Wettbewerbsfähigkeit. Zunächst einmal entfällt die Verwendung von Schalungen, also der temporären Struktur, die bei herkömmlichen Techniken verwendet wird, um den Beton bis zur Verfestigung in Form zu halten. Auch ist die Abbindezeit des verwendeten zementhaltigen Materials kürzer als die von herkömmlichem Beton. Wenn die Elemente direkt vor Ort gedruckt werden, können auch Transportkosten eingespart werden, was die Nachhaltigkeit und Effizienz des Projekts insgesamt verbessert. Der 3D-Druck erfordert bis zu 50 % weniger Material, da der Beton im Vergleich zu herkömmlichen Technologien besser verteilt und damit Abfall reduziert wird. Durch die Reduzierung der Materialmenge wird auch die Umweltbelastung in Bezug auf den CO₂-Fußabdruck verringert.
Die Geschichte des 3D-Drucks
Seit 2015 untersucht Heidelberg Materials in seinen Forschungs- und Entwicklungslaboren die 3D-Drucktechnologie mit zementhaltigen Materialien. Mit überzeugenden Ergebnissen: Der entwickelte 3D-druckbare Mörtel ist für die wichtigsten auf dem Markt erhältlichen Druckertypen geeignet. Nach dem Mischen mit Wasser ist das Material flüssig genug, um von der Mischmaschine zur Düse gepumpt und transportiert zu werden. Nach dem Extrudieren kann es sein Eigengewicht und das Gewicht der nachfolgenden Schichten tragen, ohne sich zu verformen.
Im Laufe der Jahre hat Heidelberg Materials sein Know-how und seine technischen Fähigkeiten verfeinert, um das Produkt und seine Nachhaltigkeit kontinuierlich zu verbessern. Die Forschungs- und Entwicklungslabore sind mit einem 3D-Drucker ausgestattet, um das im Laufe des Druckprozesses entwickelte Material zu testen und zu validieren. An dem Forschungsprojekt war ein multidisziplinäres Team aus den Bereichen Ingenieurwesen, Materialchemie, Architektur und Technik beteiligt, das insgesamt etwa 15 Personen umfasste und über 15.000 Forschungsstunden leistete.

3D-gedruckte Stütze.
Heidelberg Materials
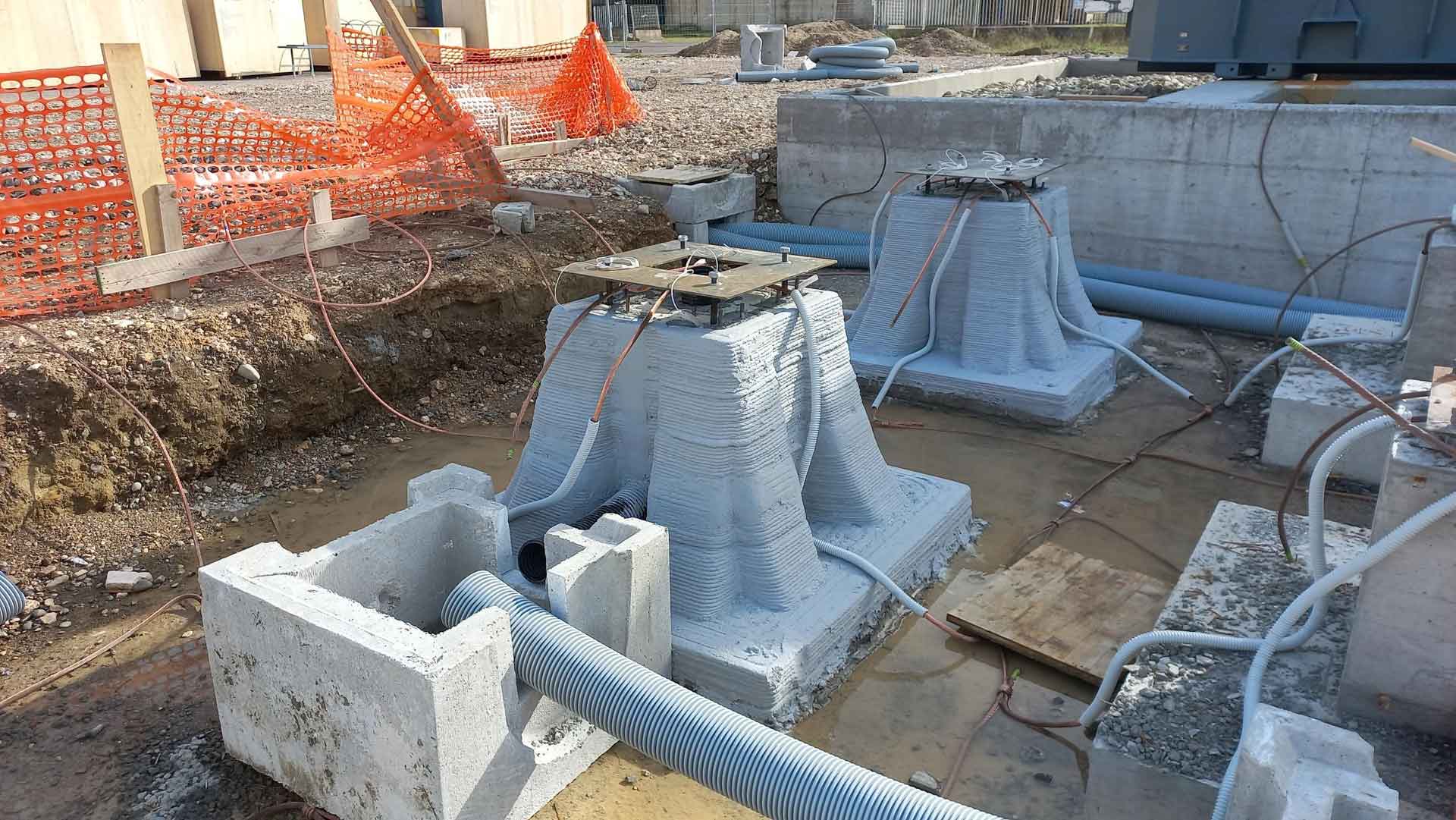
3D-gedruckte Stützen.
Heidelberg Materials

3D-gedruckte Wand.
Heidelberg Materials
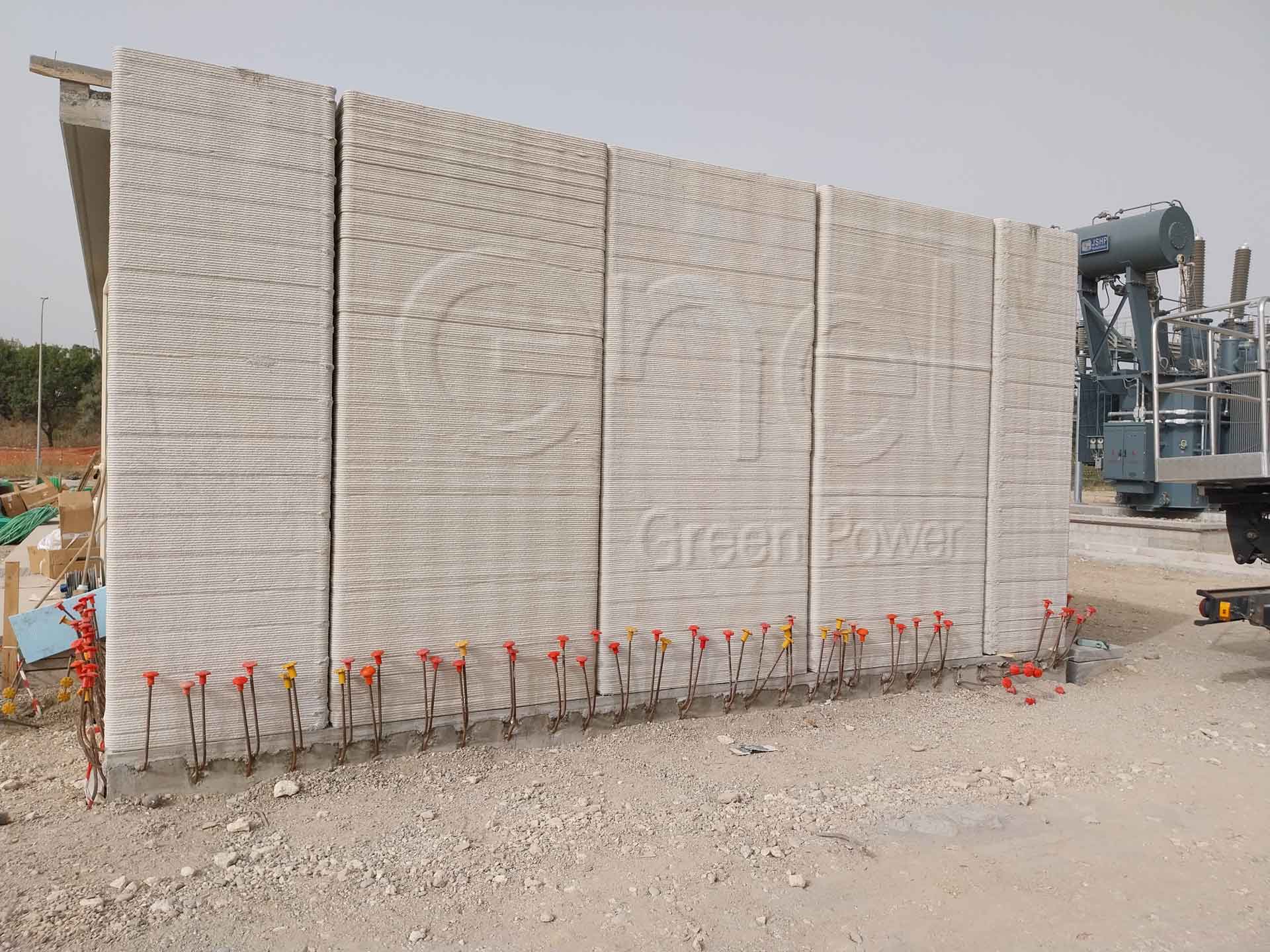
3D-gedruckte Tafel.
Heidelberg Materials
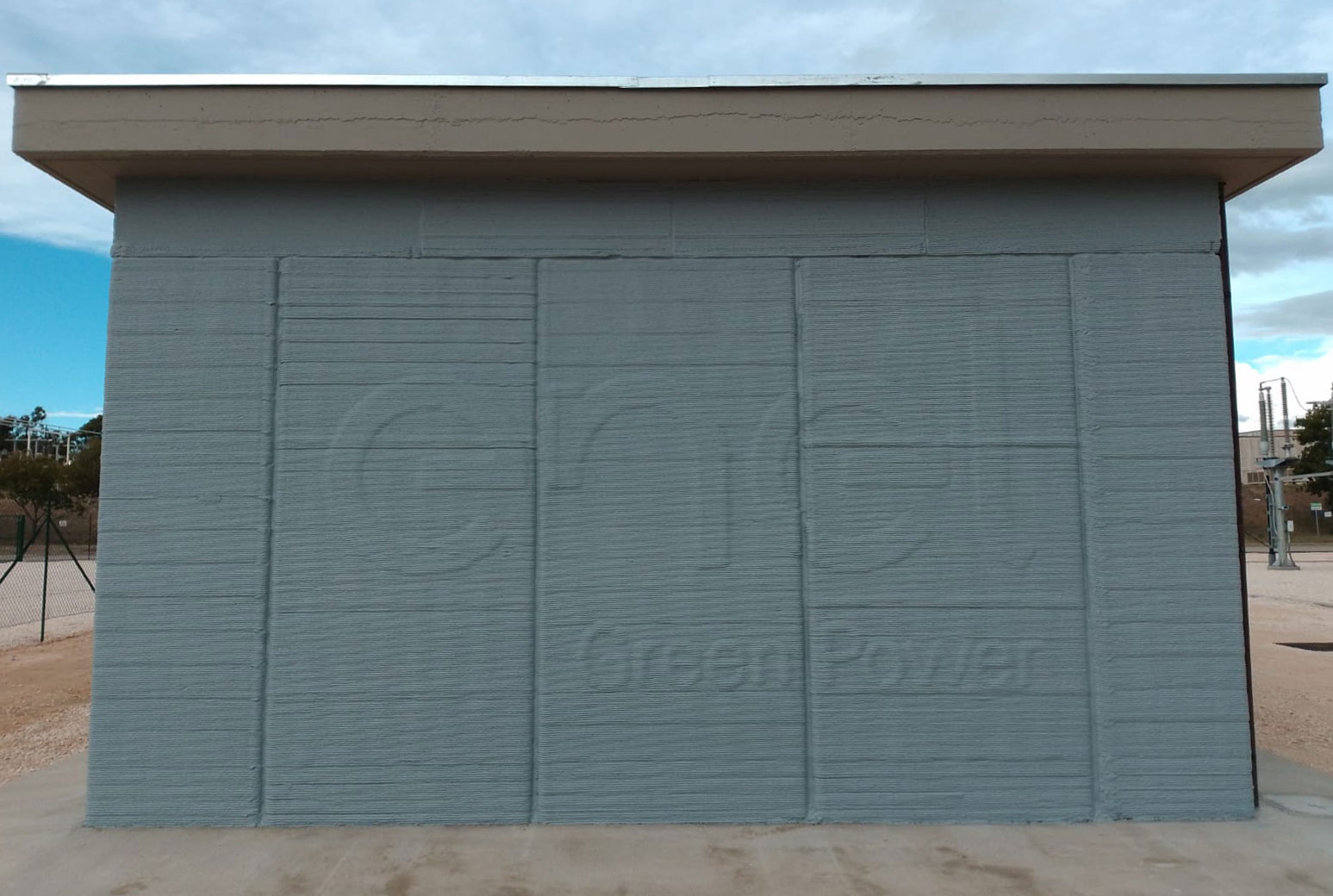
3D-gedrucktes Gebäude, Seitenansicht.
Heidelberg Materials
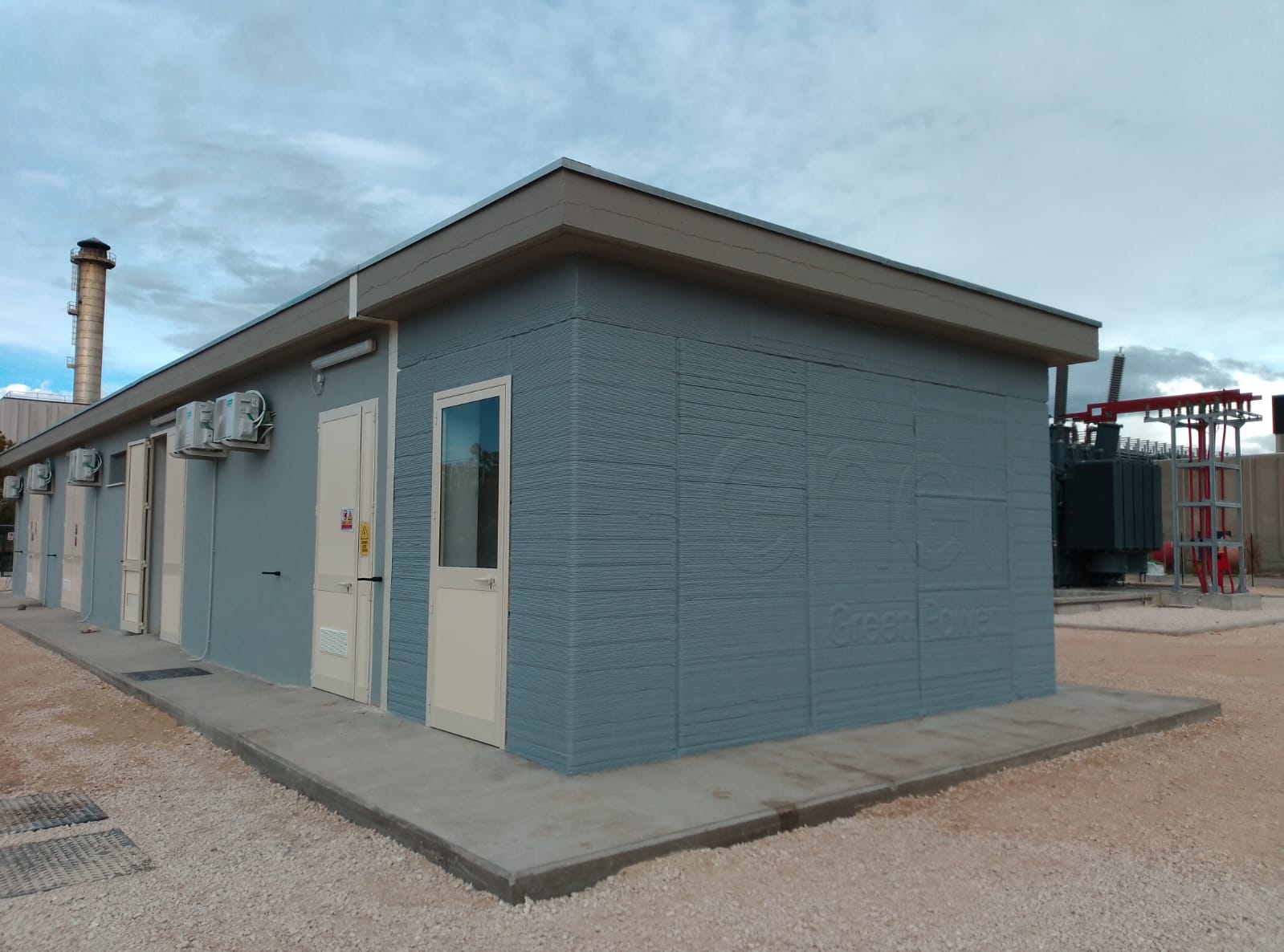
Fertiges 3D-gedrucktes Gebäude.
Heidelberg Materials

3D-gedruckte Stütze.
Heidelberg Materials
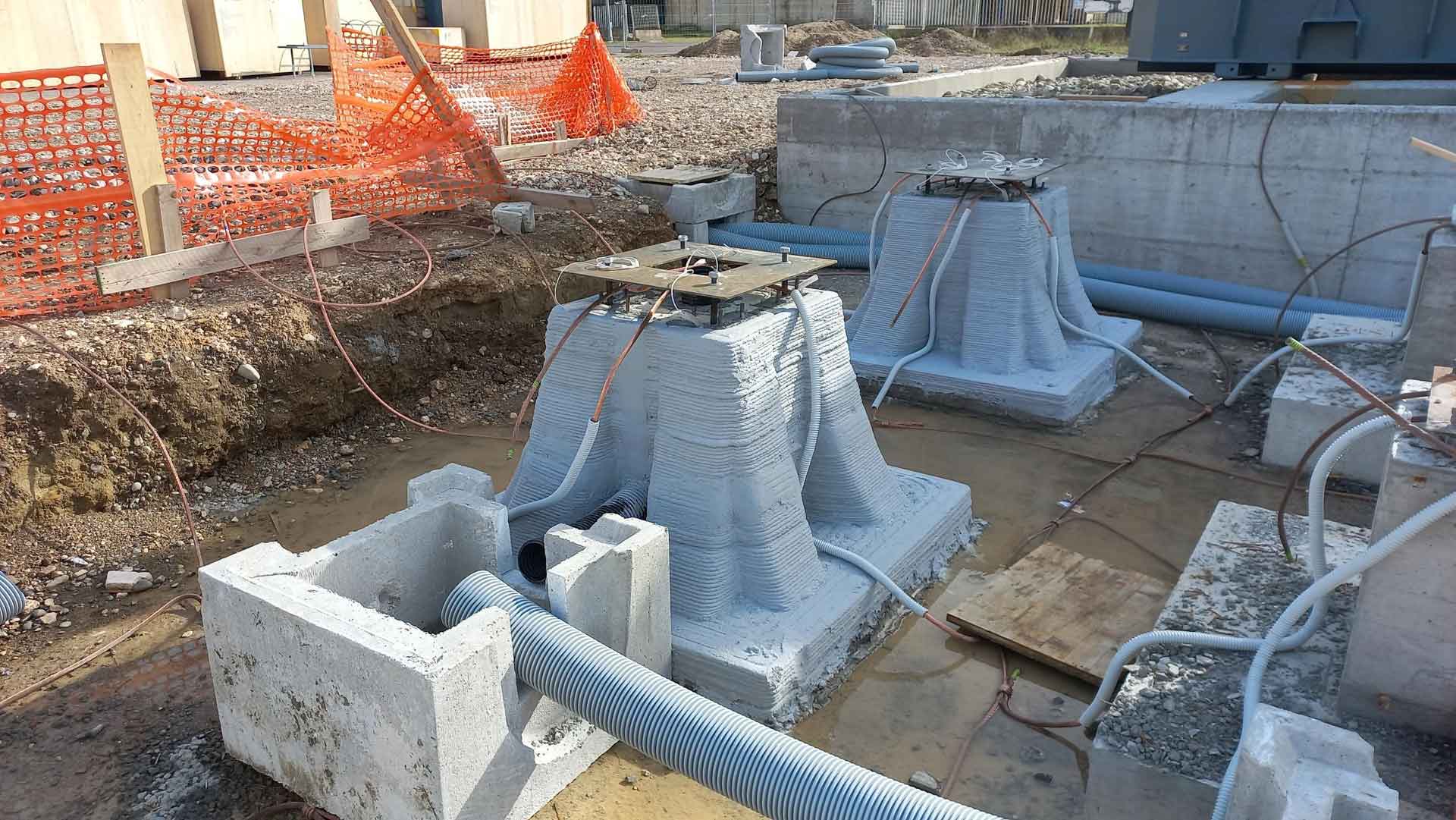
3D-gedruckte Stützen.
Heidelberg Materials

3D-gedruckte Wand.
Heidelberg Materials
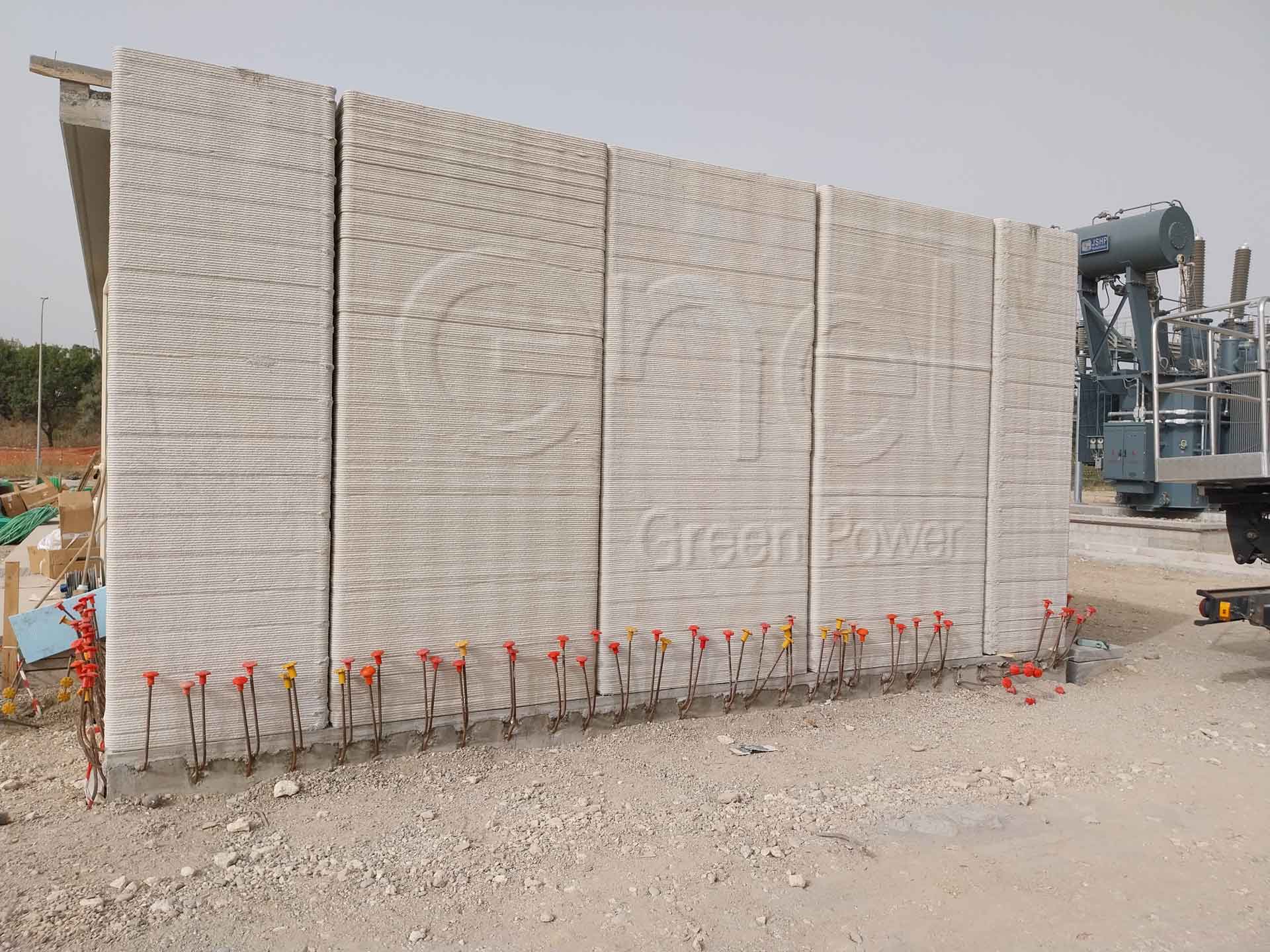
3D-gedruckte Tafel.
Heidelberg Materials
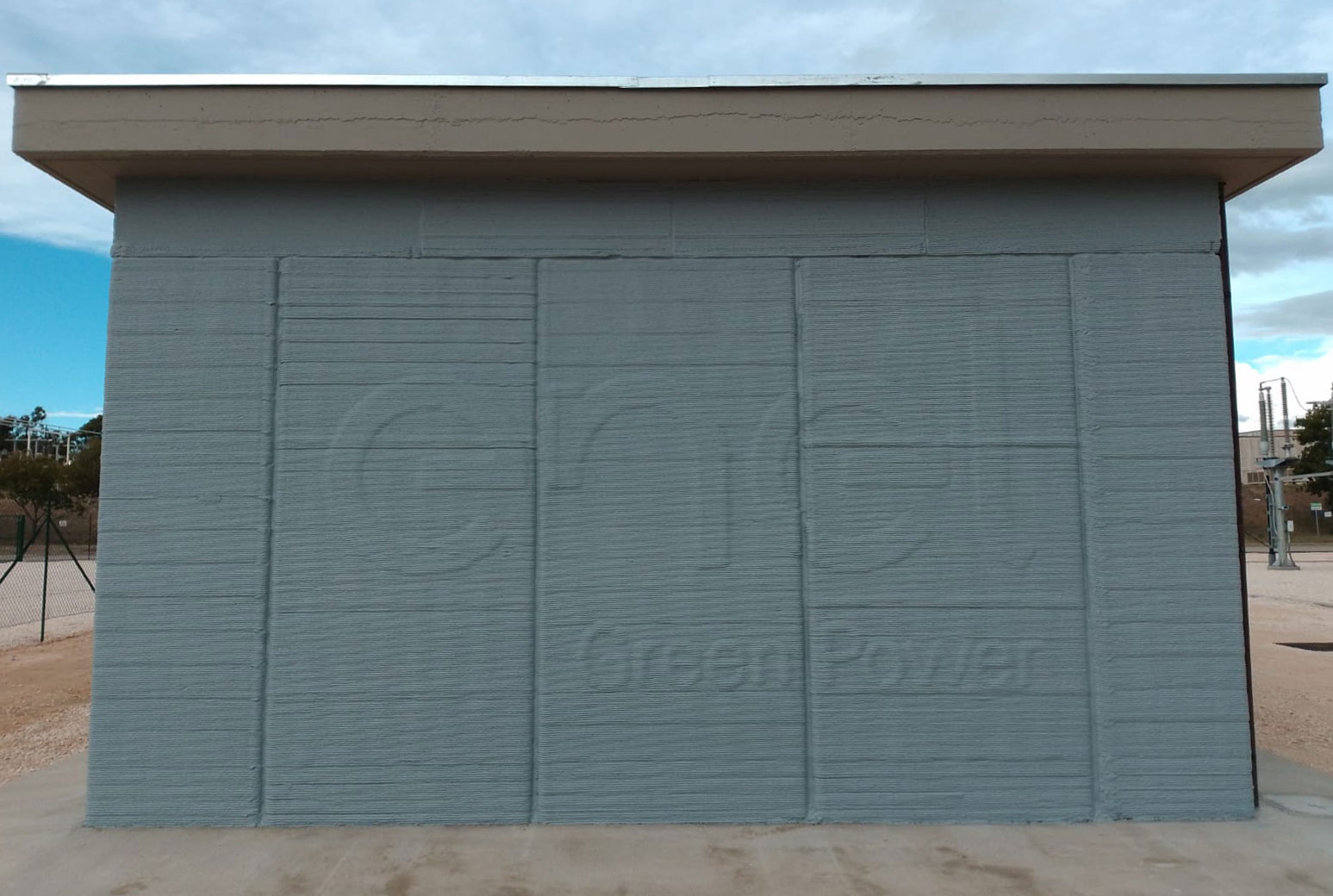
3D-gedrucktes Gebäude, Seitenansicht.
Heidelberg Materials
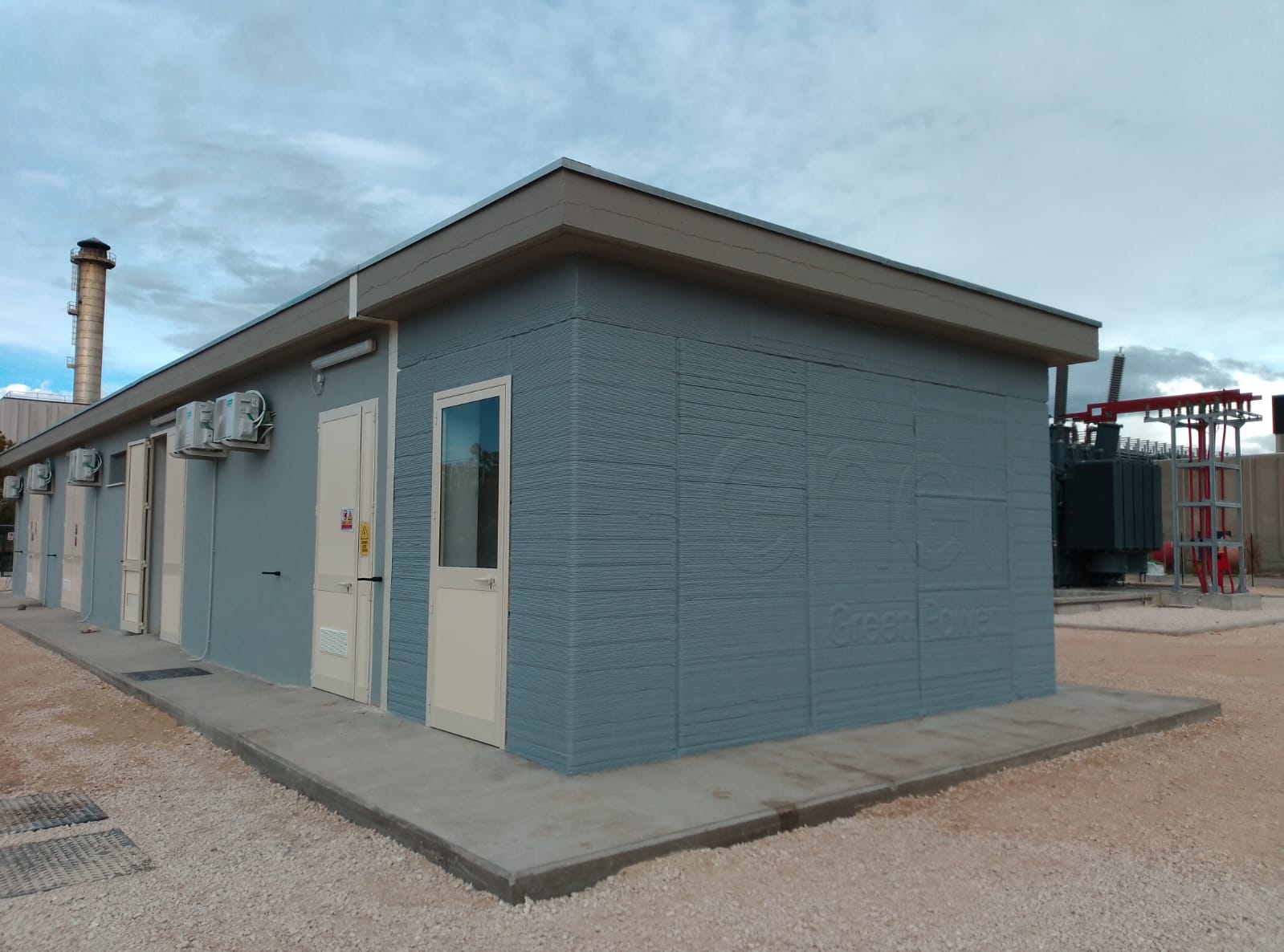
Fertiges 3D-gedrucktes Gebäude.
Heidelberg Materials