Betonrecycling auf ganz neuem Niveau
Wer die Infrastruktur der Zukunft bauen möchte, braucht dafür Beton. Er bildet buchstäblich die Fundamente unserer Straßen, Häuser, Büros und der Städte, in denen wir leben. Er bietet zahlreiche Vorteile: Beton ist langlebig, erschwinglich und wird vor Ort hergestellt. Das Bindemittel im Beton ist Zement. Ihn herzustellen, ist jedoch CO₂-intensiv.
Um die Auswirkungen, die unsere Produkte auf Klima und Umwelt haben, weiter zu reduzieren, setzen wir verschiedene Hebel ein. So kommen wir unserem Ziel zu Netto-Null-Emissionen bis 2050 immer näher. Das ist jedoch keine leichte Aufgabe. Ein Hauptbestandteil von Zement ist nämlich Klinker. Um ihn herzustellen, brennen wir Kalkstein bei sehr hohen Temperaturen. Dabei entstehen zwei Drittel der CO₂-Emissionen – diese sind unvermeidbar.
Innovative Technologien auf dem Weg zu Netto-Null
Um den CO₂-Fußabdruck unserer Prozesse und Produkte zu verringern, brauchen wir skalierbare und kosteneffiziente Technologien. Wir testen derzeit unseren firmeneigenen ReConcrete-Ansatz, der neuartige Technologien nutzt, um mehrere Herausforderungen gleichzeitig zu bewältigen:
- Recycling von Beton durch selektive Trennung, wodurch wir 100 % in der Betonproduktion wiederverwenden können
- Abscheidung und Speicherung unvermeidbarer CO₂-Prozessemissionen durch erzwungene Karbonatisierung
In diesem Artikel werden wir die Vorteile von ReConcrete erläutern: Mit ReConcrete können wir den Materialkreislauf schließen und gleichzeitig die Menge an CO₂, die in die Atmosphäre freigesetzt wird, aktiv reduzieren.
Die Grenzen des konventionellen Recyclings
Beton besteht hauptsächlich aus einer Mischung aus Zement, Wasser und Zuschlagstoffen (z. B. Sand und Kies). Am Ende der Nutzungsdauer eines Gebäudes kann Beton zurückgewonnen und wieder verwertet werden. Beim herkömmlichen Recycling wird Beton von anderen Bau- und Abbruchabfällen getrennt und anschließend weiter zerkleinert und gesiebt, um grobe und feine Stücke voneinander zu trennen. Allerdings haftet immer noch eine erhebliche Menge Zementstein am Sand und Kies.
Wenn dieser unerwünschte Bestandteil im Frischbeton wiederverwendet wird, nimmt er sehr viel Wasser auf. Dies erhöht den Bedarf an Zement und Zusatzstoffen, was sich wiederum auf die Gesamtqualität auswirkt. Außerdem verringert der Zementstein die Festigkeit der Gesteinskörnung. Ebenso haben die feinen Bestandteile der wiedergewonnenen Materialien als recyceltes Material wenig bis keinen Wert.
Deshalb wird Abbruchbeton in der Regel zerkleinert, ohne ihn zu sieben. Das entstehende Granulat wird dann für den Straßenunterbau oder für Erdarbeiten verwendet. Dies ist zwar immer noch besser als ihn auf die Deponie zu bringen, nutzt aber nicht das eigentliche Potenzial des Materials für die Herstellung von Frischbeton oder Zement und lässt somit erhebliche CO₂-Einsparmöglichkeiten ungenutzt.
Die hohe Kunst des Betonrecyclings
Unser Forschungsteam machte sich auf die Suche nach innovativen Ansätzen und geeigneten Geräten, um den Zementstein effektiv von Sand und Kies zu trennen. Sie fanden eine Lösung in einem Verarbeitungsverfahren, das Scherkräfte nutzt und damit deutlich weniger Druck ausübt, um die Oberfläche der Sand- und Kieskörner vom Zementstein zu befreien.
Gemeinsam mit einem unserer Lieferanten entwickelten sie ein geeignetes Verfahren weiter und optimierten die Maschinen, um eine bahnbrechende Lösung für das Recycling von Beton und Zement zu entwickeln. Seitdem wir die Geräte an die Bedürfnisse unserer Branche angepasst haben, können wir Sand gewinnen, der nahezu die gleichen Produkteigenschaften wie das Naturmaterial aufweist. Somit können wir große Mengen and Sand für Beton wiederaufbereiten.
Bei den gröberen Bestandteilen, dem Kies, lieferte unser Verfahren sogar noch bessere Ergebnisse – mit potenziellen Ersatzraten von bis zu 100 % ohne Qualitätsverlust. Nach ersten erfolgreichen Versuchen wusste unser Forschungsteam, dass es einen wichtigen Meilenstein auf dem Weg zur Schließung des Materialkreislaufs für Sand und Kies erreicht hatte.
Selektive Trennung vorantreiben
Im Juli 2024 eröffneten wir in der Nähe von Katowice, Polen, eine weltweit einzigartige Recyclinganlage für die selektive Trennung. So konnten wir die neue Recyclingtechnologie im industriellen Maßstab einführen und testen. Durch eine verbesserte Trennung und Sortierung von Abbruchmaterial sind wir nun in der Lage, Beton ohne Qualitätsverlust vollständig zu recyceln und bei der Betonherstellung so weit wie möglich neue Materialien zu ersetzen.
Während Sand und Kies nun ihre ursprünglichen Pendants ersetzen können, stellt sich die Frage, was mit dem Zementstein geschieht. Im Gegensatz zur herkömmlichen Methode, bei der Beton einfach zerkleinert wird, wird alter Beton durch selektive Trennung effizient in alle seine ursprünglichen Bestandteile zerlegt: Neben hochwertigem Kies und Sand gewinnen wir nun auch den Zementstein in Form von feinem Pulver, das als recycelte Betonpaste (RCP) bezeichnet wird. Im Weichmahlverfahren wird der Zementstein aufgebrochen und von den Oberflächen von Kies und Sand abgerieben. Der Prozess ist vollständig mechanisch und trocken, was Kosten reduziert und zu einer einfachen Umsetzbarkeit führt.
Neue Wege zur Reduzierung von CO₂
Das nun separat gewonnene RCP, das traditionell eigentlich als eine an recycelten Zuschlagstoffen haftende Verunreinigung angesehen wird, bietet in mehrfacher Hinsicht ein erhebliches Dekarbonisierungspotenzial.
Da RCP bereits fein gemahlen ist, kann es bei der Betonherstellung einfach dem Rohstoffgemisch beigemischt werden, wodurch Kalkstein teilweise ersetzt und CO₂-Emissionen im Prozess eingespart werden. Bei einem typischen industriellen RCP aus einer normalerweise karbonatisierten Betonstruktur können somit etwa 150 kg CO₂ pro Tonne RCP vermieden werden.
Noch interessanter ist, dass sich das wiedergewonnene RCP als besonders wertvoll erwies und über den Ersatz von Neumaterialien hinausgeht. Durch eine erzwungene Karbonatisierung können wir zusätzliche CO₂-Einsparungen erzielen. Um diese Technologie außerhalb der Laborumgebung zu erforschen, bauen wir derzeit in unserem Zementwerk in Górażdże, Polen, eine industrielle Demonstrationsanlage für die erzwungene Karbonatisierung. Das durch selektive Trennung in der nahe gelegenen Recyclinganlage gewonnene RCP wird demnächst zur Demonstrationsanlage in Górażdże transportiert.
Erzwungene Karbonatisierung in Kürze
Der Zementstein bindet auf natürliche Weise CO₂. So wirkt Beton über seinen gesamten Lebenszyklus als CO₂-Senke und trägt dazu bei, 20 % der bei seiner Herstellung verursachten Emissionen auszugleichen. In Betonstrukturen ist dieser Prozess absichtlich langsam, um eine Korrosion der Stahlbewehrung zu verhindern.
Mit der beschleunigten Karbonatisierung nutzen wir diese grundlegende Eigenschaft und beschleunigen sie. Anstatt das RCP auf natürliche Weise in der Umgebungsluft karbonatisieren zu lassen, setzen wir das Pulver unseren eigenen Ofengasen aus der Zementproduktion aus, die etwa 20 Prozent CO₂ enthalten. Dadurch können wir die Karbonatisierung viel schneller erreichen. Labor- und Industrieversuche haben gezeigt, dass eine praktisch vollständige Karbonatisierung in weniger als einer halben Stunde erreicht werden kann.
Die Karbonatisierungsreaktion ist spontan und erfordert keine externe Energiezufuhr. Dies macht sie – verglichen mit Alternativen – zu einer sehr effizienten Technologie zur CO₂-Abscheidung und -speicherung (CCS). In unserer Branche wird CCS zunehmend getestet und angewandt, um zu verhindern, dass die unvermeidbaren CO₂-Prozessemissionen in die Atmosphäre gelangen.
RCP kann aber noch für weitere Zwecke eingesetzt werden: Nach der Karbonatisierung wird es zu einem reaktiven Material, das als Zusatzstoff für Zement (SCM) Klinker in Kompositzementen ersetzen kann. Auf diese Weise können weitere 750–850 kg CO₂ pro Tonne RCP vermieden werden. Insgesamt hat die erzwungene Karbonatisierung mit der CO₂-Bindung einerseits und dem Klinkerersatz andererseits das Potenzial, eine Tonne CO₂ pro Tonne RCP einzusparen.
Ein Blick in die Zukunft
Wir erreichen nun eine entscheidende Phase, in der sich unsere Pilotprojekte auf die Validierung unseres ReConcrete-Ansatzes im industriellen und kommerziellen Maßstab konzentrieren. Mit einer Kapazität von bis zu 100 Tonnen Beton pro Stunde sind wir das erste Unternehmen der Branche, das eine hochwertige selektive Betontrennung in dieser Größenordnung einführt. Die baldige Fertigstellung unserer industriellen Pilotanlage für die verstärkte Karbonatisierung markiert einen weiteren wichtigen Meilenstein für ReConcrete, für den wir 2022 mit dem Deutschen Innovationspreis für Klima und Umwelt ausgezeichnet wurden.
Schon damals war die Jury beeindruckt von dem enormen Potenzial, die CO₂-Emissionen deutlich zu reduzieren und die Kreislaufwirtschaft im Bauwesen zu fördern. Jetzt liegt es an uns, dieses Potenzial in der Praxis in Polen und darüber hinaus nutzbar zu machen. Nur wenn große Mengen an Altbeton in verschiedenen Regionen auf sehr kosteneffiziente Weise verarbeitet werden, können wir angemessen auf die Bedürfnisse des Marktes eingehen. Damit können wir einen wichtigen Beitrag zu einer breiten Akzeptanz und Einführung einer vollwertigen Recycling- und Kreislaufbetonproduktion in unserer Branche leisten.
Downloads
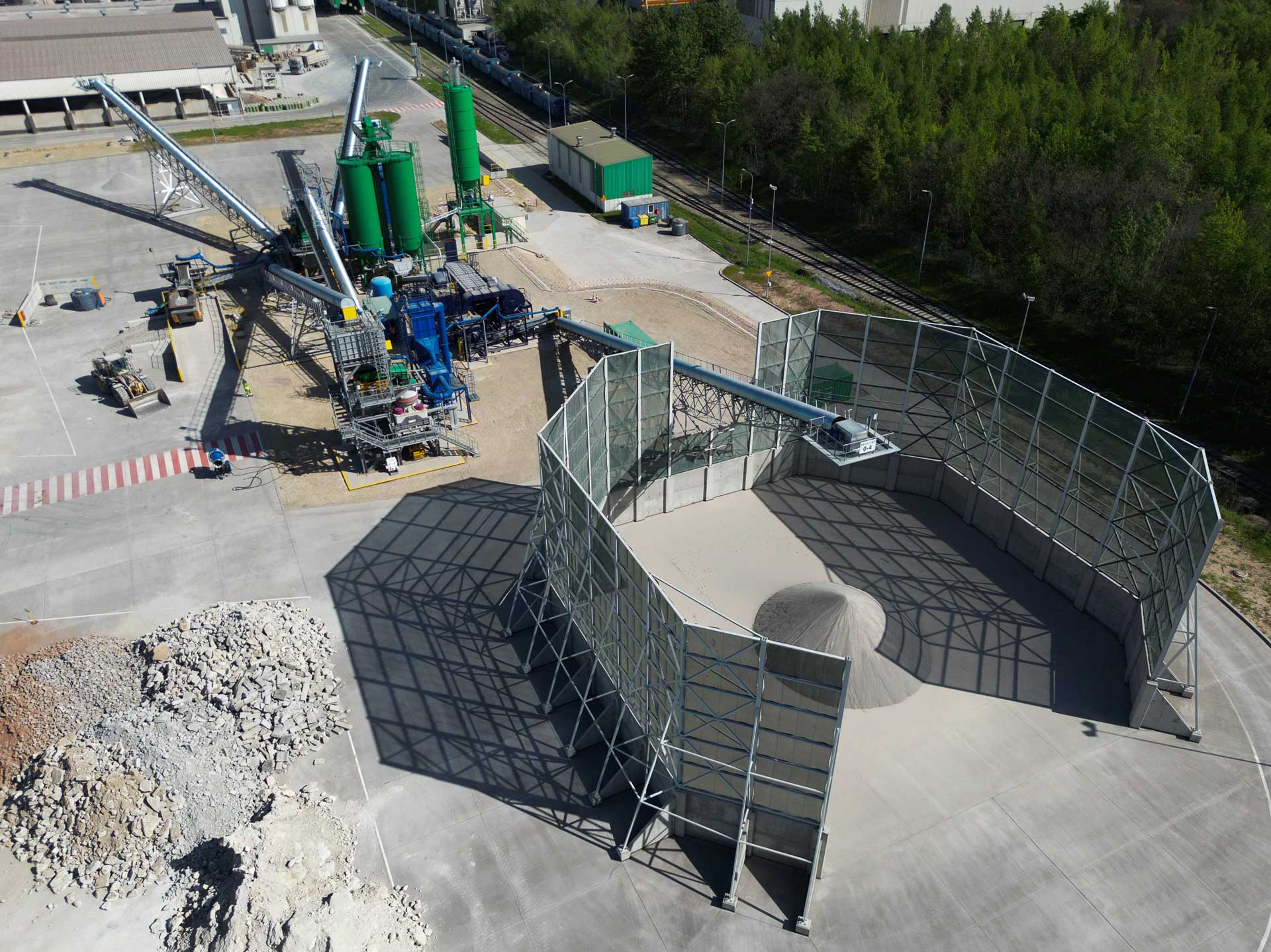
Recyclinganlage Katowice (2). Recyclinganlage im Werk von Heidelberg Materials bei Katowice, Polen
Heidelberg Materials
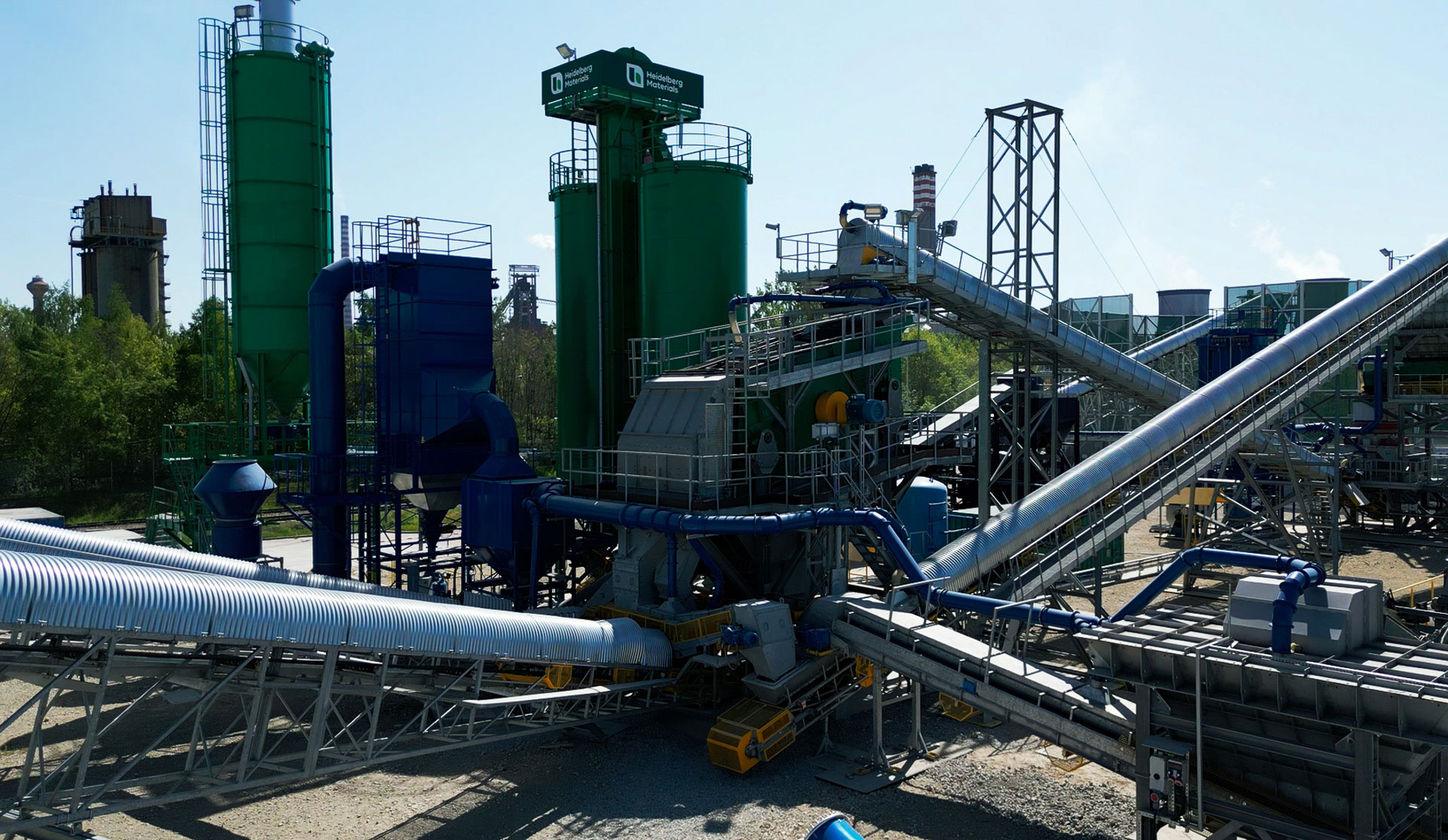
Recyclinganlage Katowice (1). Recyclinganlage im Werk von Heidelberg Materials bei Katowice, Polen
Heidelberg Materials
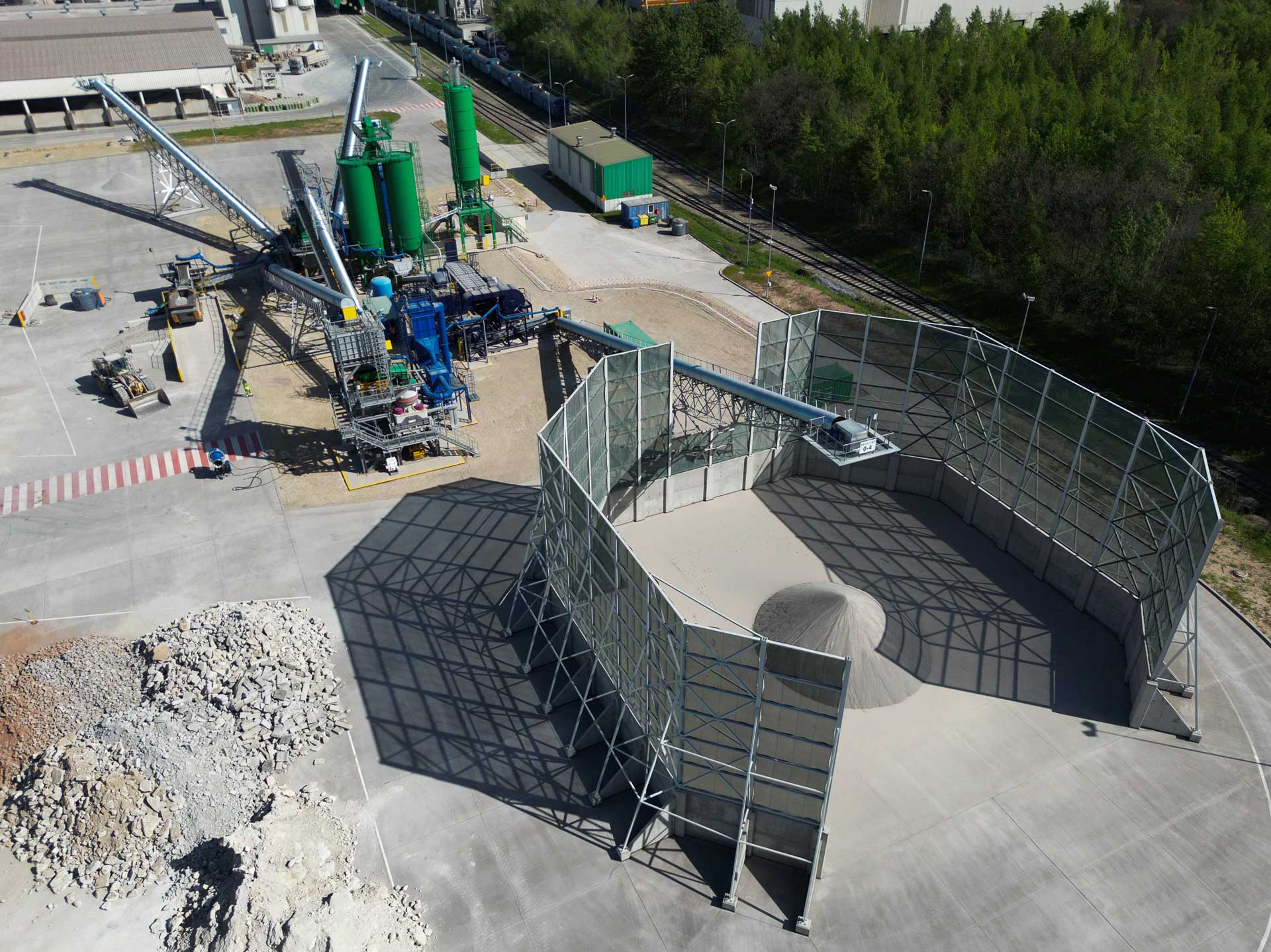
Recyclinganlage Katowice (2). Recyclinganlage im Werk von Heidelberg Materials bei Katowice, Polen
Heidelberg Materials
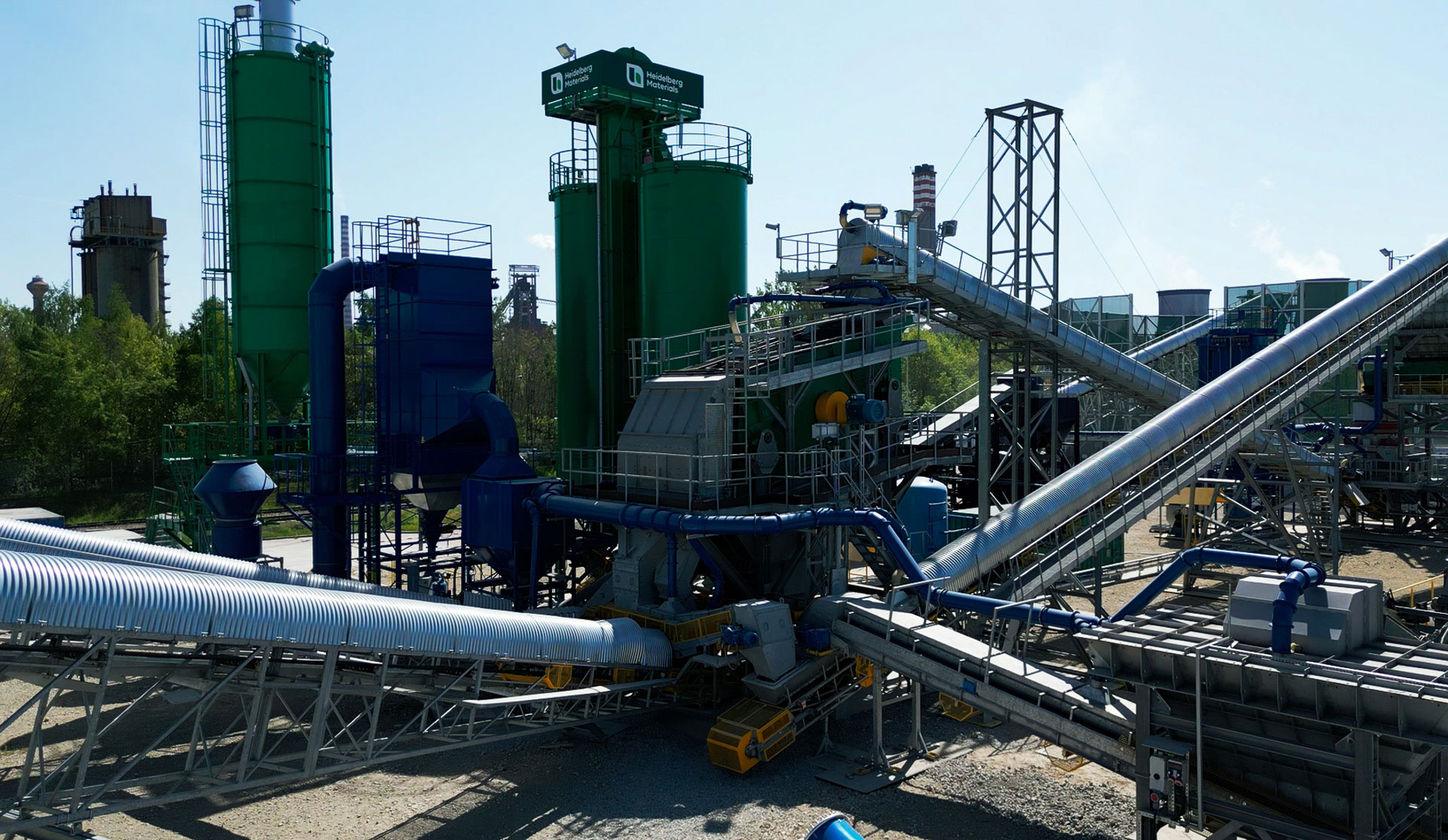
Recyclinganlage Katowice (1). Recyclinganlage im Werk von Heidelberg Materials bei Katowice, Polen
Heidelberg Materials