3D-printed earthquake resistance
First earthquake-resistant building in Italy made with 3D concrete printing
For the first time in Italy, a concrete structure has been built in a seismic zone using 3D Concrete Printing technology. Heidelberg Materials provided Enel Green Power and the University of Naples Federico II with an innovative cementitious material to print a small industrial building and a foundation system for part of the electrical equipment.
The construction will be part of a substation in the BESS (Battery Energy Storage System) plant within the Alessandro Volta power station in Montalto di Castro (Lazio, Center Italy). The prototypes created can contribute to a significant breakthrough, as this technology reduces construction times and contributes to greater sustainability in construction.
The advantages of this construction technology include its adaptability to specific needs and optimized mechanical performance.
Thanks to the high degree of digitalization, 3D printing allows for increased safety on construction sites and the ability to build structures with complex shapes and customized details that would be difficult or impossible to achieve with traditional methods,
confirms Engineer Martina Palomba, a researcher at Heidelberg Materials' Research and Development laboratories.
Each structural element was fabricated in the industrial area of Volla (Naples): here, thanks to the collaboration with the University of Naples Federico II and Etesias – a spin-off of the same University – the two foundations and walls were created and then assembled in Montalto by a team of workers, like a giant Lego set. A robotic arm printed each component by depositing a continuous filament of 3D printable material. This filament, several kilometres long, followed a pre-designed path with the help of specialized software reproducing the digital 3D model. The employed 3D printable mortar is the i.tech 3D cementitious material produced by Heidelberg Materials (the brand that inherited Italcementi's legacy in Italy). The process is almost entirely automated and requires the technical team only to verify the quality of the mixed and pumped material and control the printing parameters, such as the extrusion speed of the filament or the geometry of each block.
The Advantages of 3D Construction: Faster sites, Lower costs, and Less CO₂
Although 3D printable material is currently more expensive than traditional concrete, the construction process is much faster and more convenient: we are talking about at least a 50% time-saving. In the energy market, particularly renewable energy, being fast means being more competitive. First of all, the use of formwork (the temporary structure used in conventional techniques to contain concrete until it solidifies) is eliminated, and the setting time of the cementitious material used is shorter than that of traditional concrete. If the elements are printed directly on-site, there are also savings on transportation costs, improving the overall sustainability and efficiency of the project. This system also requires less material (up to about 50% less) because 3D printing optimizes the distribution of concrete compared to traditional technologies and reduces waste. By reducing the amount of material, there is also a lower environmental impact in terms of CO₂ footprint.
The History of 3D Printing
Since 2015, Heidelberg Materials has been studying 3D printing technology with cementitious materials at its Research and Innovation laboratories. The results have been significant: the 3D printable mortar developed is suitable for the main types of printers available on the market. Once mixed with water, the material is fluid enough to be pumped and transported from the mixing machine to the nozzle, but once extruded, it can support its self-weight and the weight of subsequent layers without deforming.
Over the years, Heidelberg Materials has refined its know-how and technical skills to continuously improve the product and its sustainability. The Research and Development laboratories are equipped with a 3D printer to test and validate the material developed throughout the printing process. The research project involved a multidisciplinary team of engineers, material chemists, architects, and technicians, totalling about 15 people and over 15,000 hours of research.

3D-printed pillar.
Heidelberg Materials
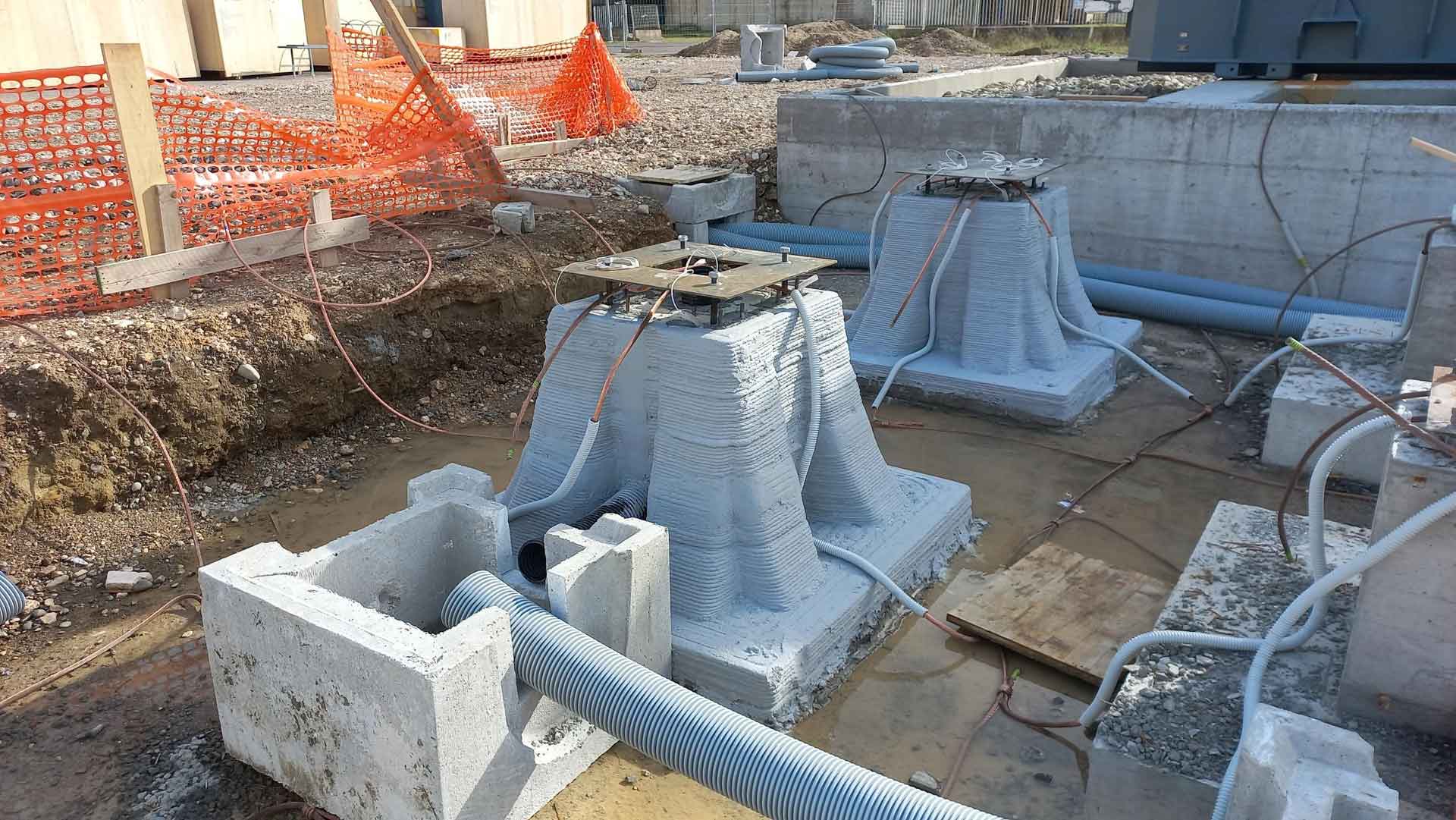
3D-printed pillars.
Heidelberg Materials

3D-printed wall.
Heidelberg Materials
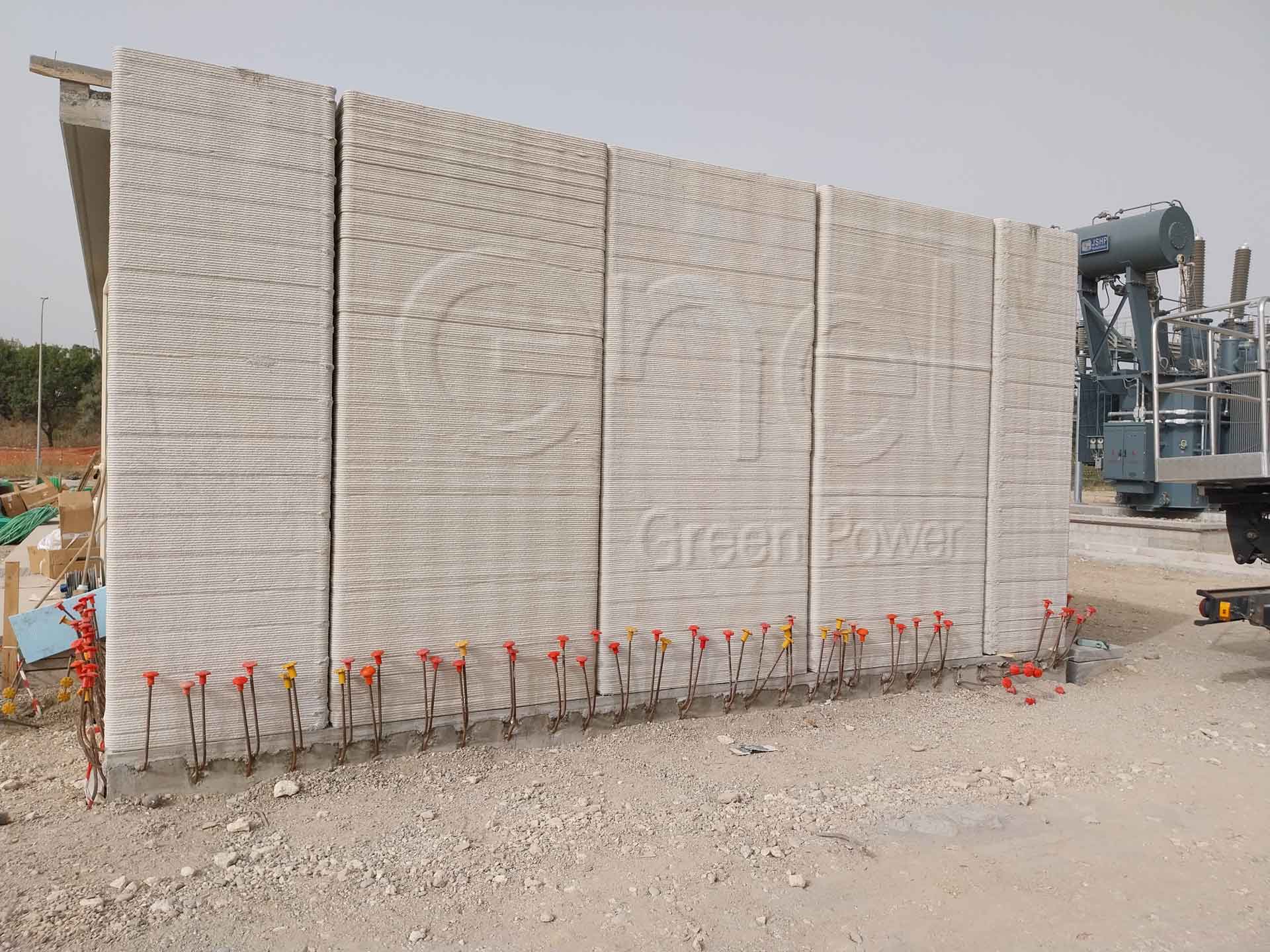
3D-printed table.
Heidelberg Materials
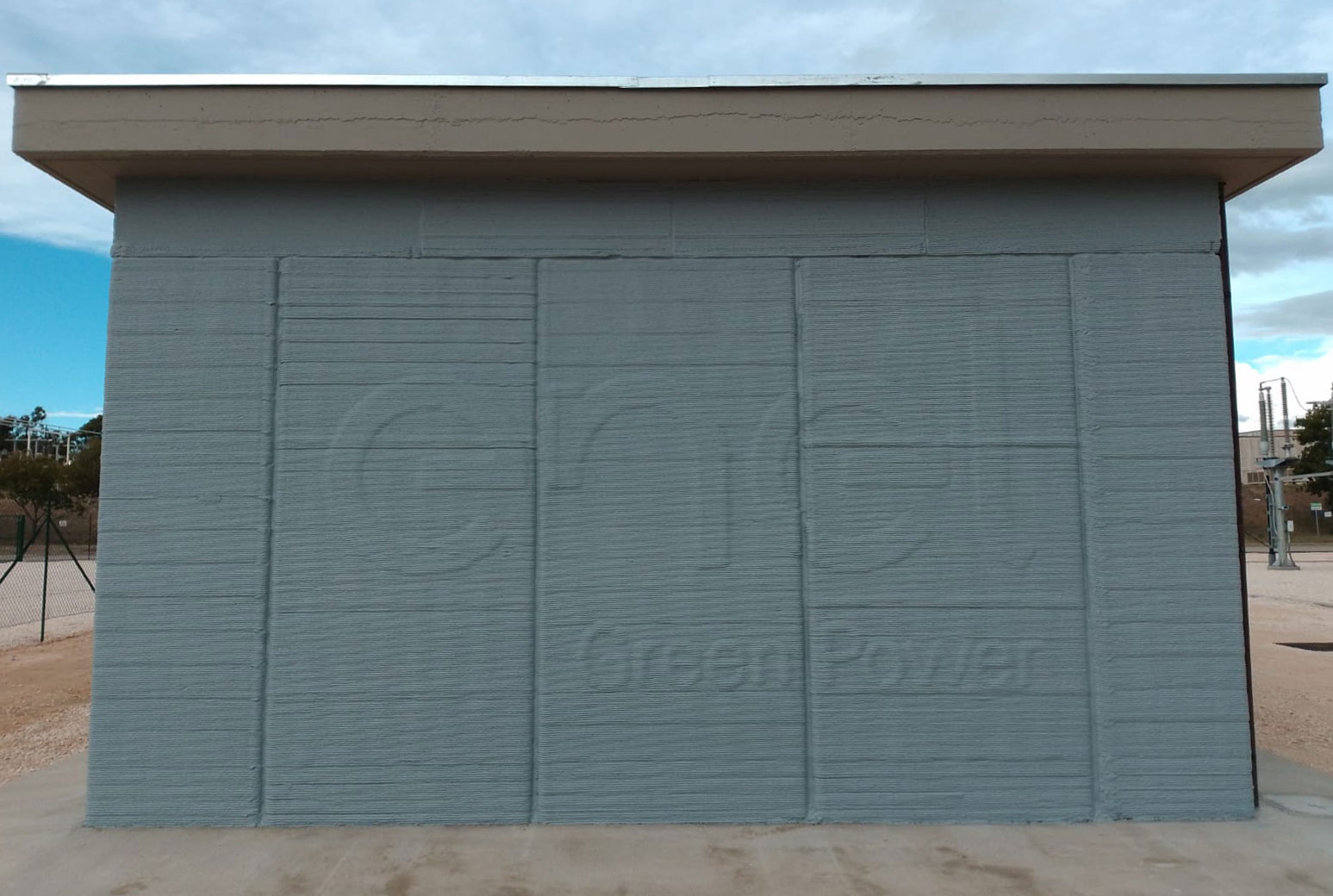
3D-printed building, side view.
Heidelberg Materials
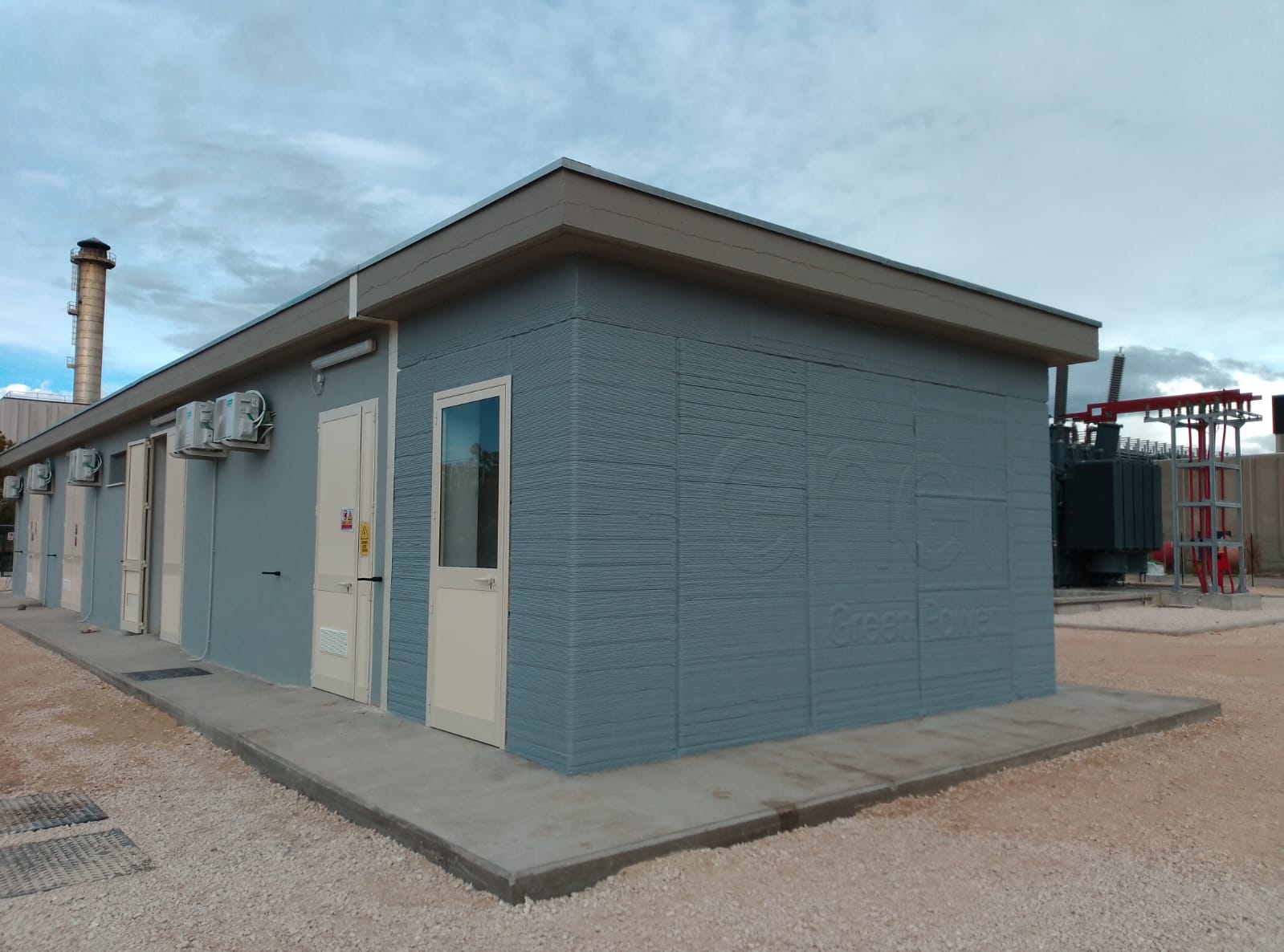
Finished 3D-printed building.
Heidelberg Materials

3D-printed pillar.
Heidelberg Materials
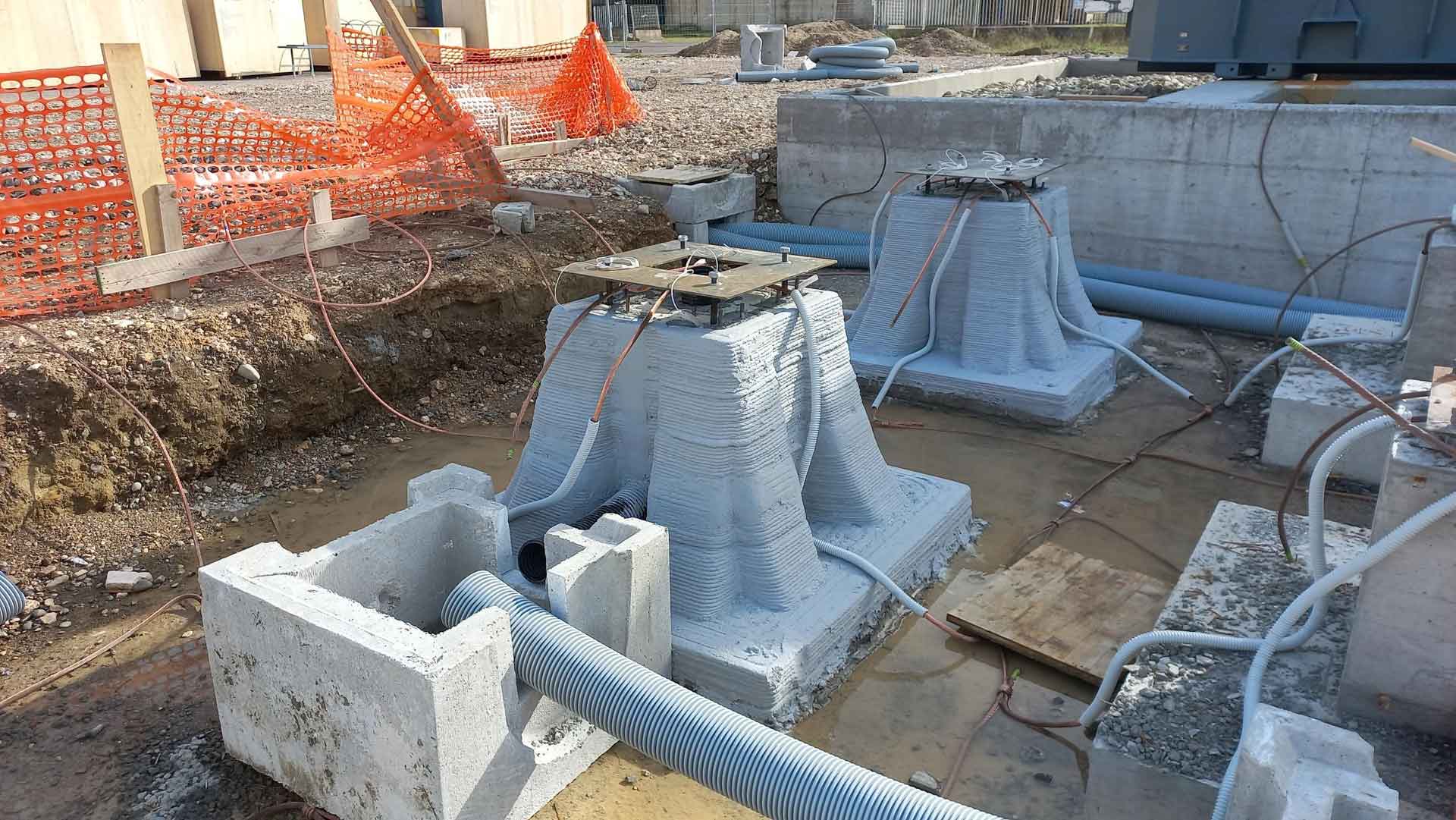
3D-printed pillars.
Heidelberg Materials

3D-printed wall.
Heidelberg Materials
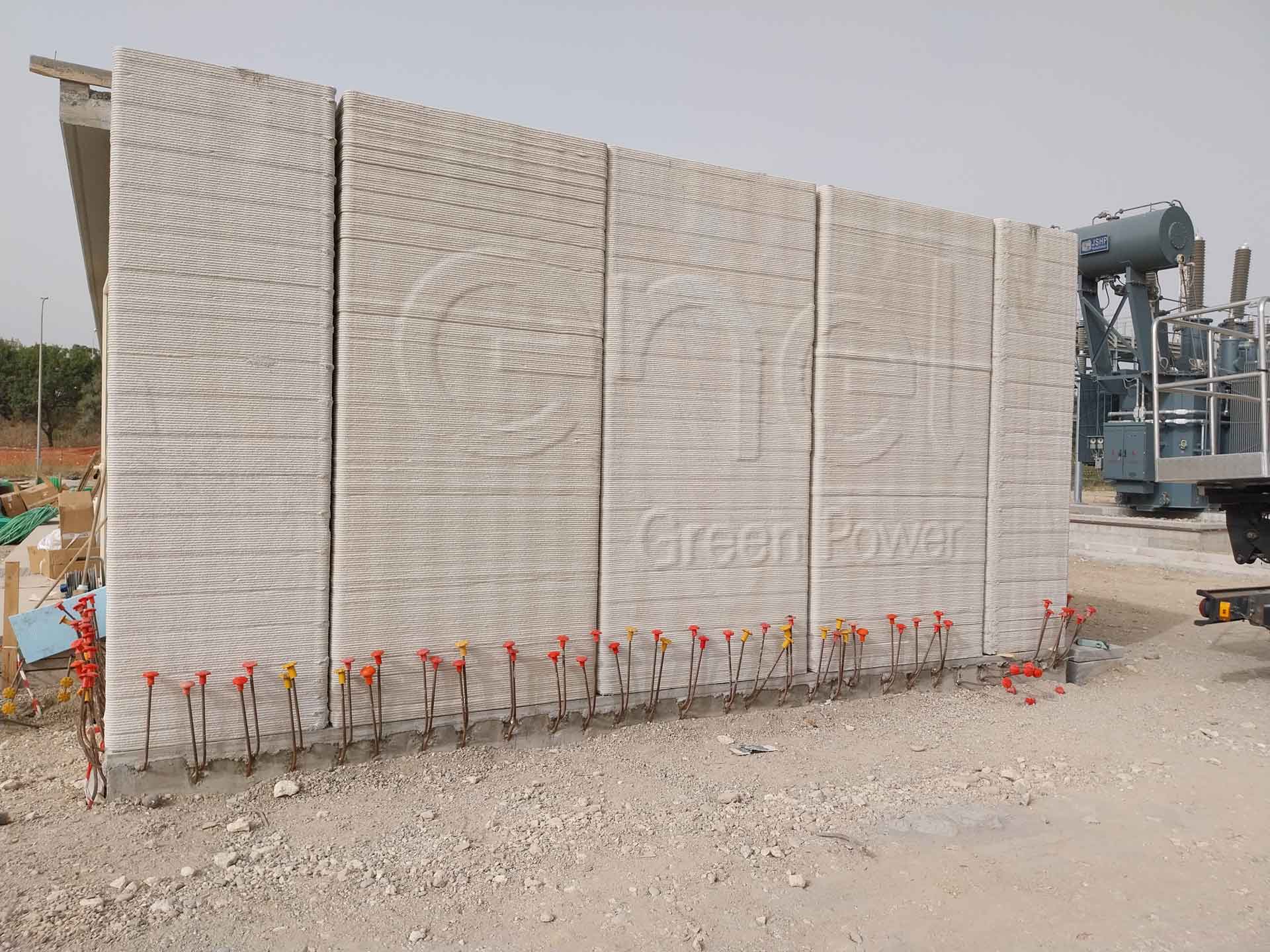
3D-printed table.
Heidelberg Materials
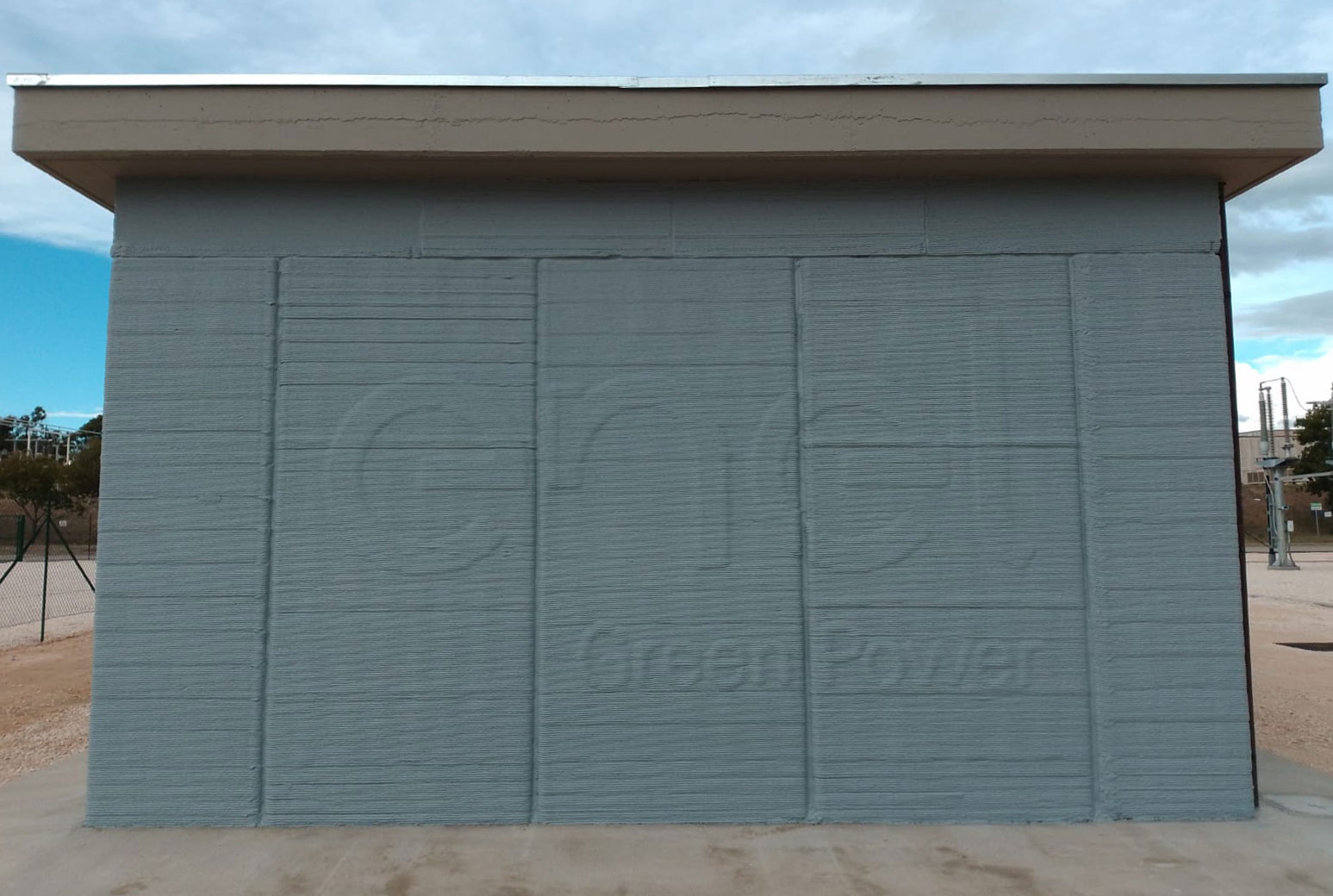
3D-printed building, side view.
Heidelberg Materials
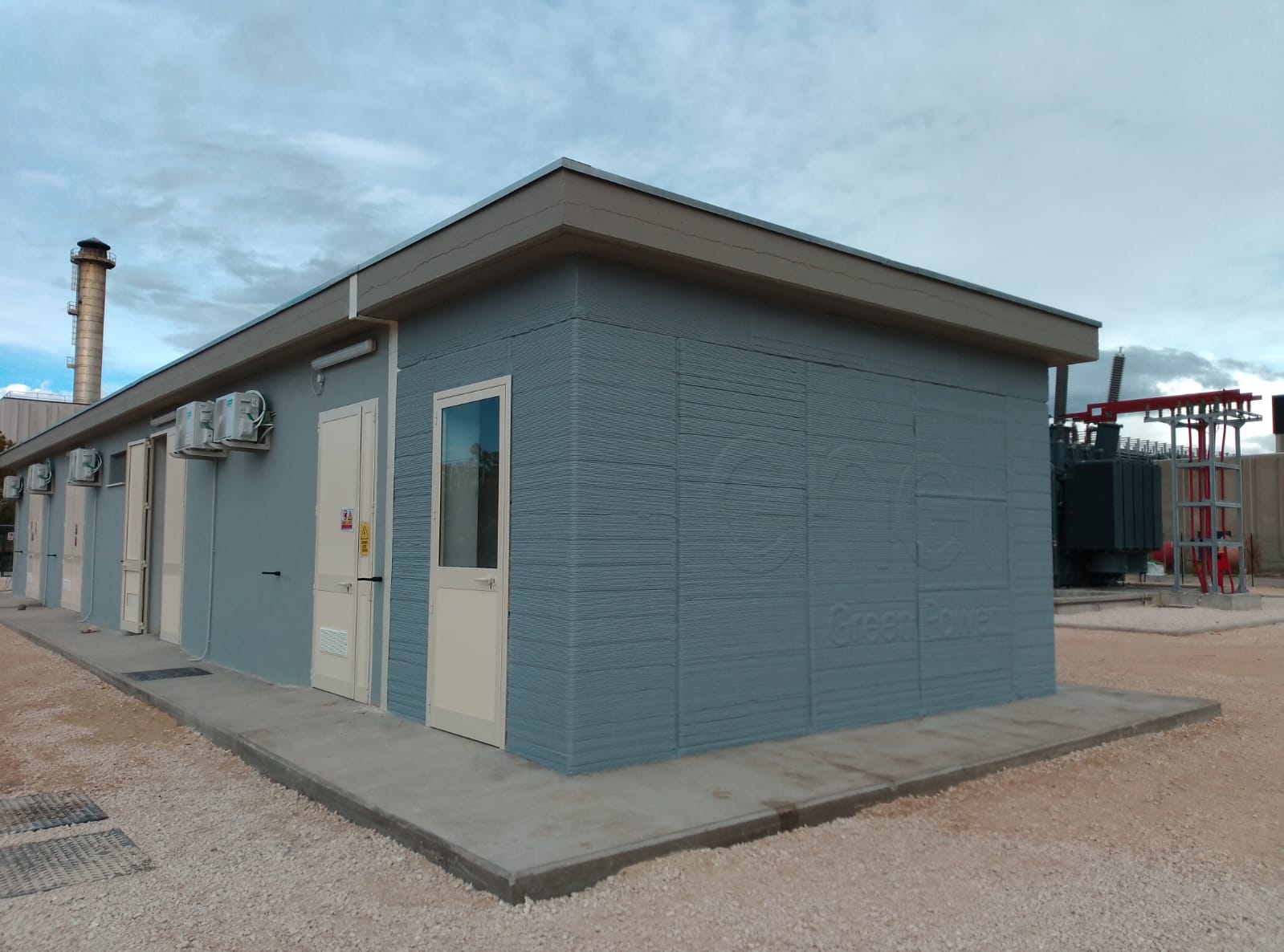
Finished 3D-printed building.
Heidelberg Materials