How a plant in Skövde adapted to Sweden’s electricity market volatility
Smart production planning
- At the Heidelberg Materials cement plant in Skövde, an industrious city in Sweden with the charm of a small town, a significant challenge has been tackled with the help of digital solutions and smart leadership. Alexander Lagerholm, the production manager, led his team into new territory as the once predictable electric market in Sweden encountered the effects of market shifts.
Facing the turbulence
For a long time, Alexander’s operations ran smoothly, backed by the consistent and low electricity prices in Sweden. However, changes in the national power supply and export policies, coupled with the impact of the war in Ukraine, meant that stability was a thing of the past.
"It was hard for us to predict the electrical costs and time-consuming to gather data on stock levels and dispatch,” Alexander says, reflecting on how the plant initially struggled with the sudden market changes. With more frequent mill start-ups and shutdowns, operational processes had to be quickly reevaluated.
From whiteboard to digital
The search for a solution led to the Production Planning & Optimizer, a feature within the Digital Cement Operations suite of digital tools. Alexander appreciated the user-friendly interface and how the feature allowed more informed electricity usage and production planning.
It helped the plant shift from a static weekly schedule to dynamic, data-driven daily planning. "Before, we planned weekly on a whiteboard in the control room. Now, we often change the plan in the mornings, with new data such as electricity prices and silo levels to optimise all parameters. Also, information is sent electronically to the control room giving the operators a better overview,” Alexander explains.
As a result, planning now takes just a few minutes each day, and the energy bill in January–May 2023 saw a consistent decrease of 2–8% each month.
Co-creating success
The successful implementation of the Production Planning & Optimizer was a collective achievement, born out of close collaboration with Digital Cement Operations research and development team. Input from Alexander and his team played a role in adapting the tool to meet Skövde's operational needs.
„All markets differ, but we had a lot of says regarding how we in Scandinavia plan our production," recalls Alexander, emphasizing the user-centred design process that accommodated the specific needs of the region.
Greener footprint
The effects of adopting the new planning tool extend beyond immediate operational improvements. "It helps the electrical system and grid minimise peak consumption of electricity. We can show external stakeholders that we are a part of the solution, not only the problem,” Alexander points out, emphasizing that the plant can now shift its energy use to times when the grid is less strained and more renewable energy is available. This strategy not only reduces costs but also supports the use of greener energy.
Eyes are now set on the next phase of development, with anticipation for features like raw material planning and annual budgeting that will further consolidate planning operations.
Welcome to the digital transformation
To anyone wondering whether to adopt this innovative approach, Alexander Lagerholm has some advice:
Save costs, and why not with an internal Heidelberg Materials tool that is world-class?
The story of Skövde's cement plant is more than just a struggle with a shifting power market. It is about embracing change through digital solutions, thoughtful leadership, and a determination to pursue both operational excellence and sustainability. It shows how adaptive strategies can help you thrive in the face of uncertainty.
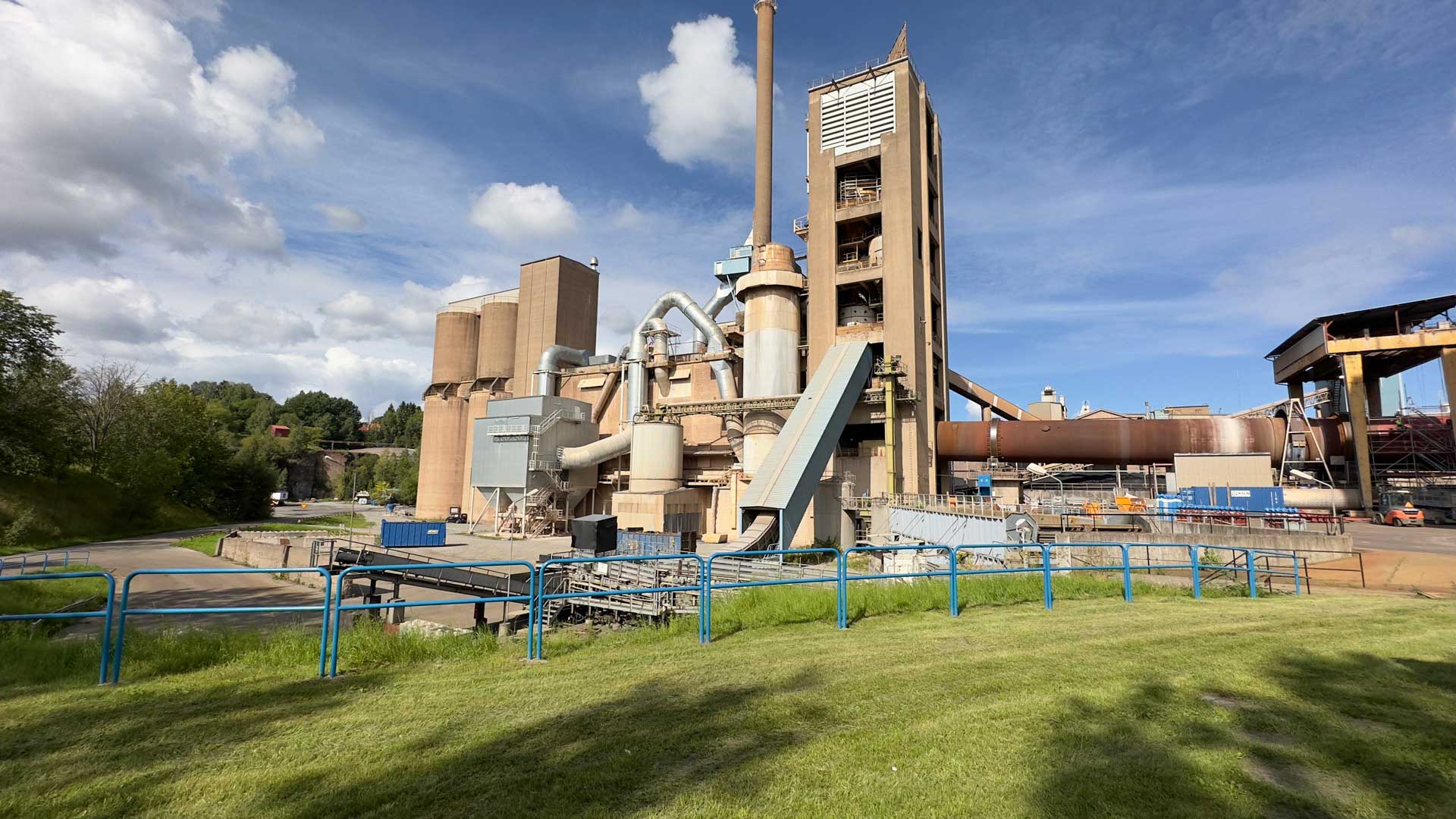
Plant Skövde.
Heidelberg Materials
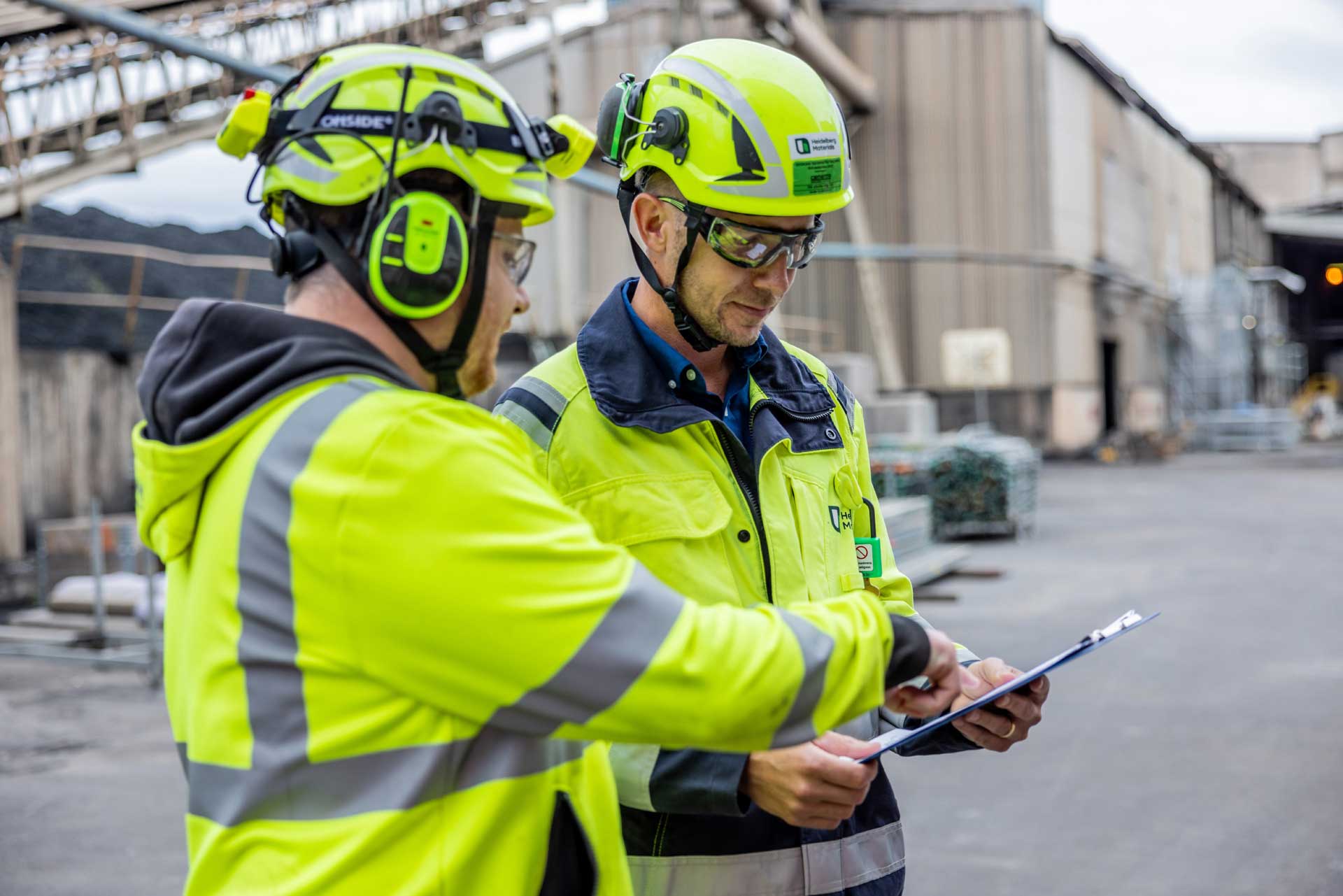
Employees Skövde.
Heidelberg Materials
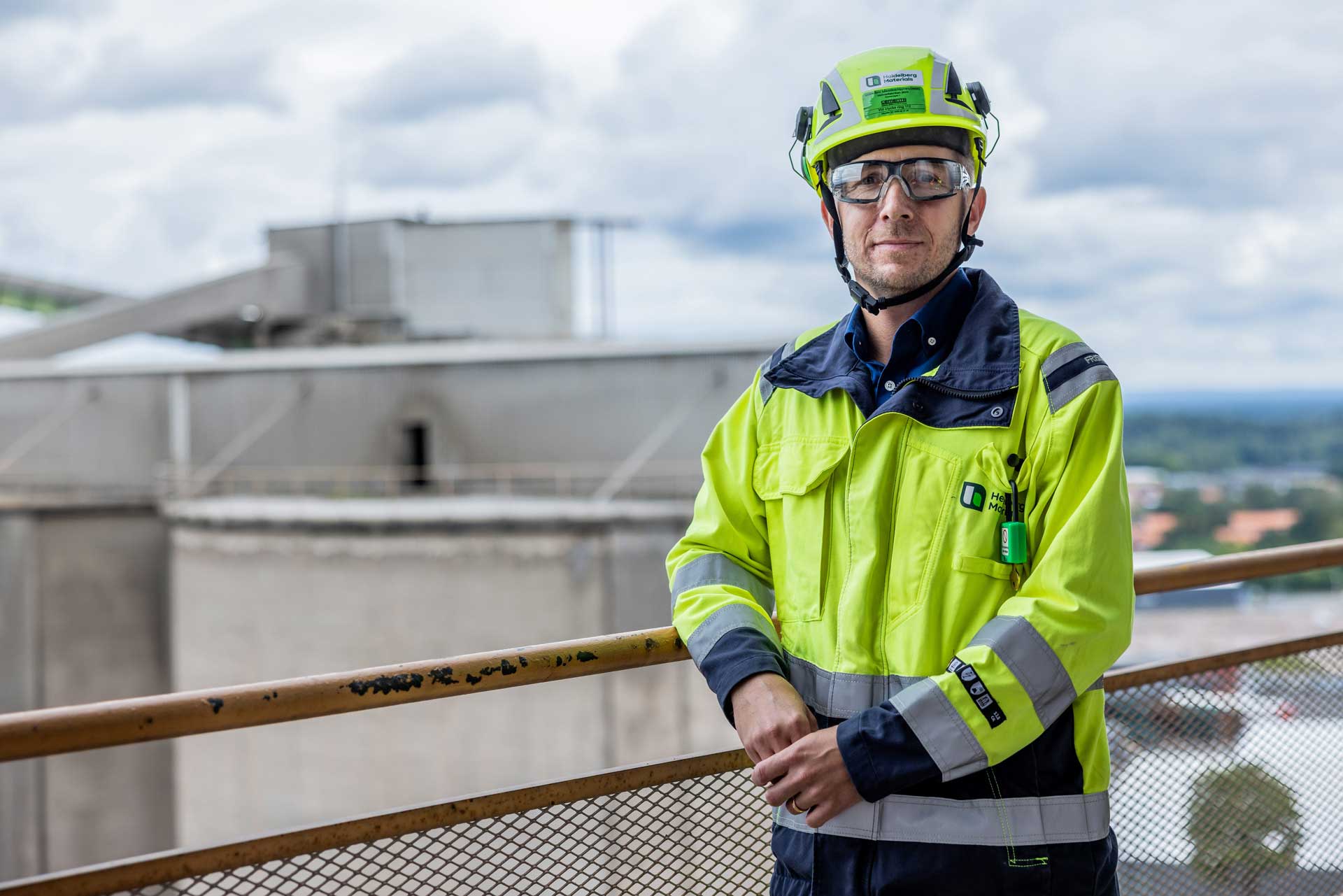
Employee Skövde.
Heidelberg Materials
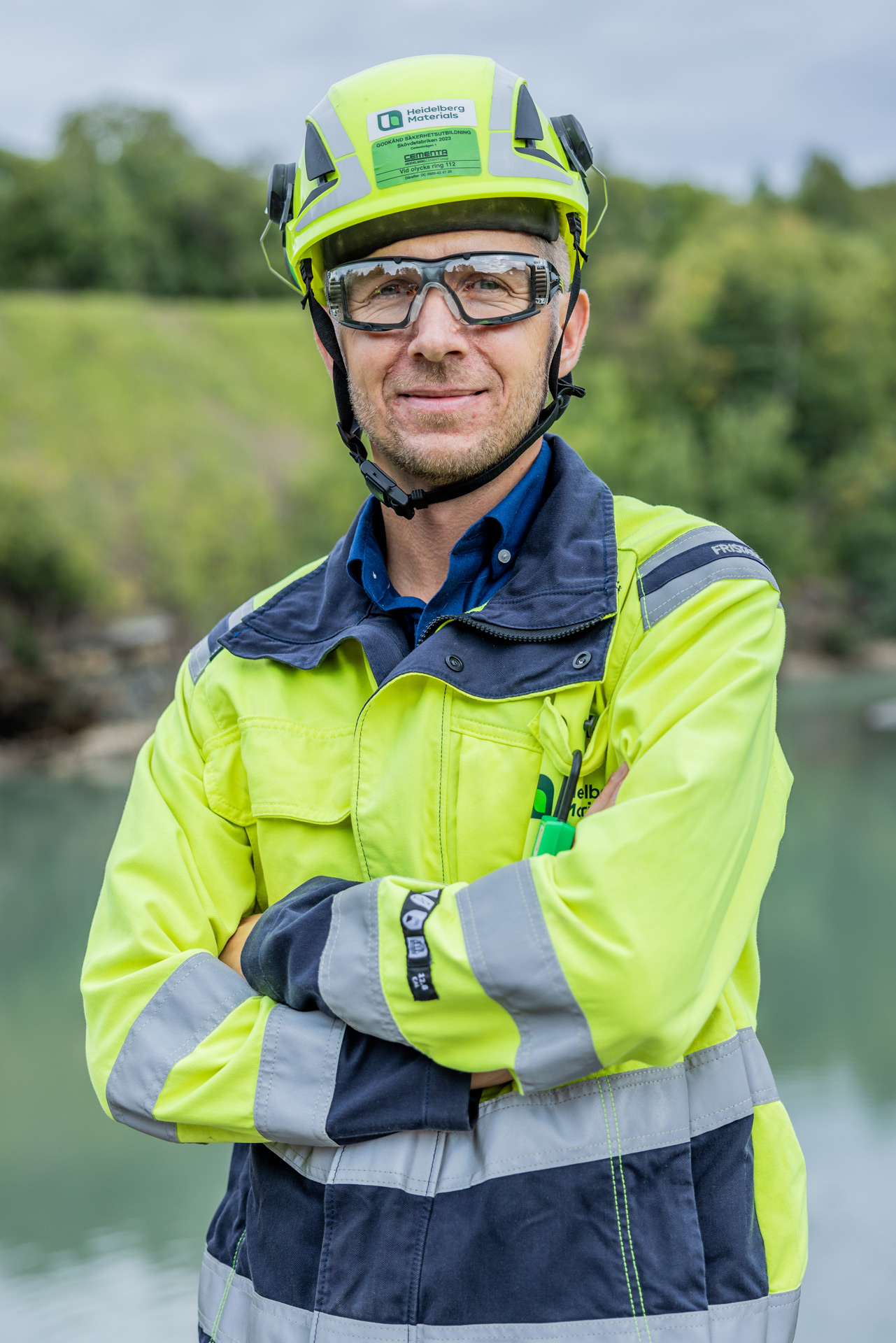
Employee Skövde.
Heidelberg Materials
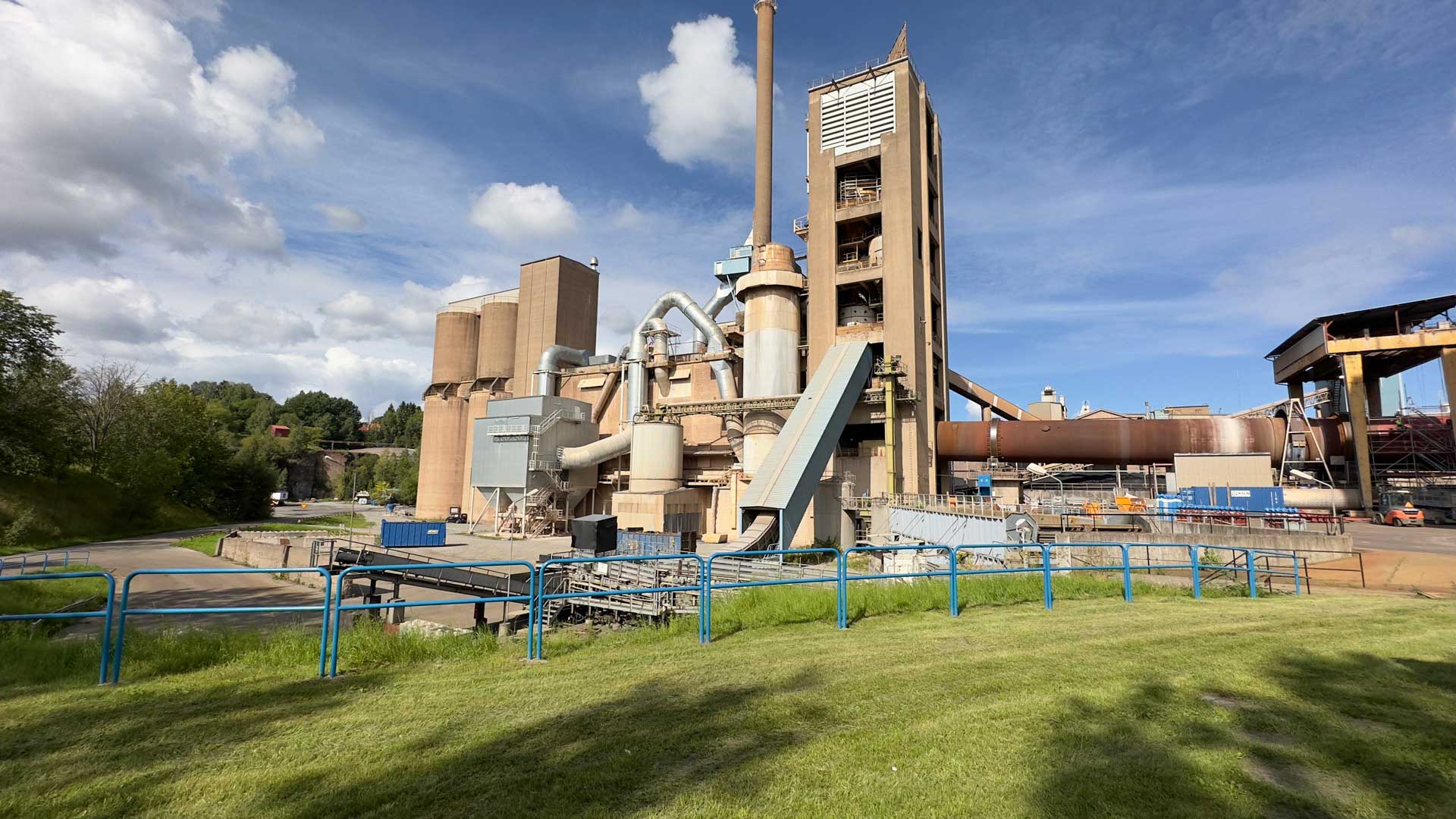
Plant Skövde.
Heidelberg Materials
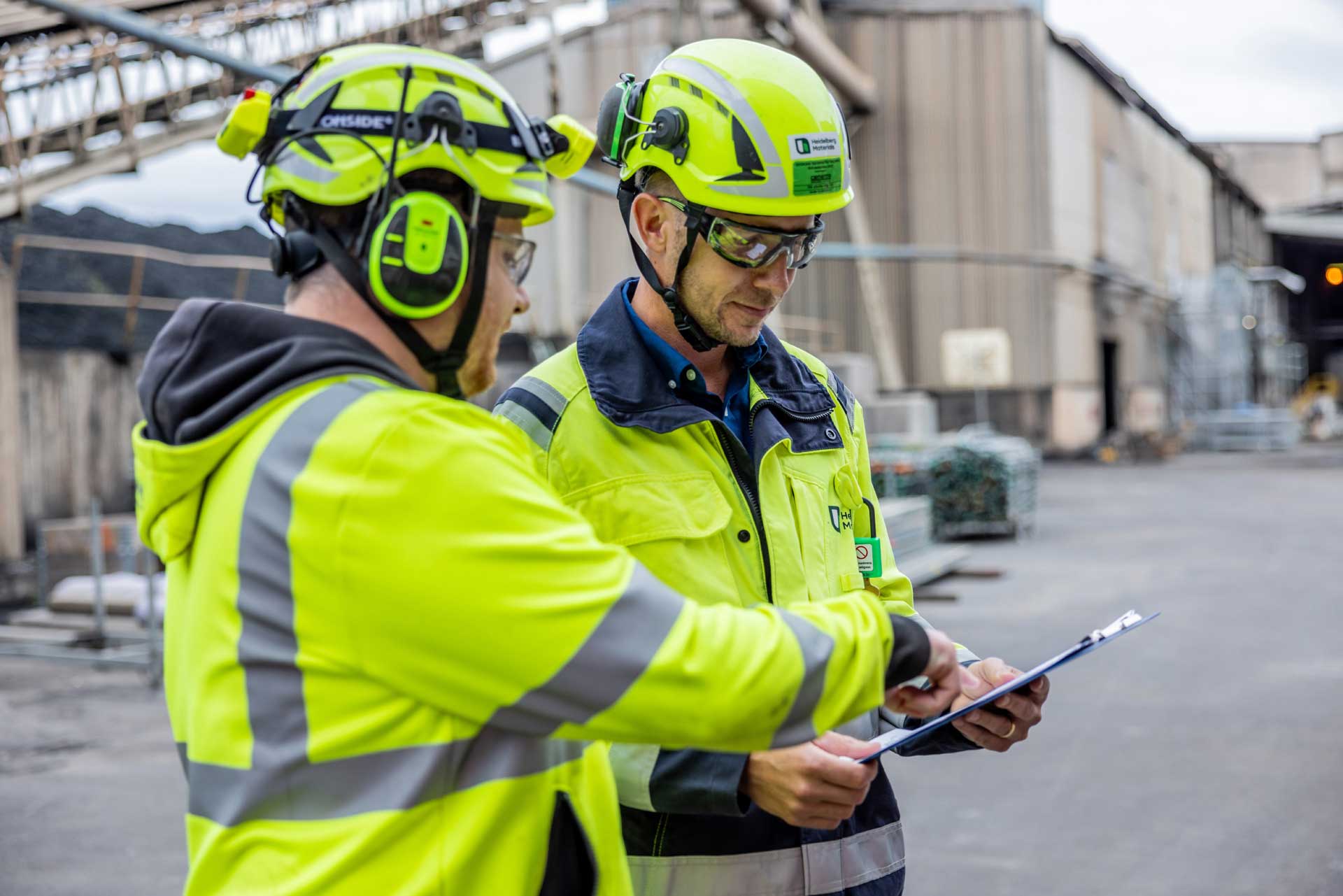
Employees Skövde.
Heidelberg Materials
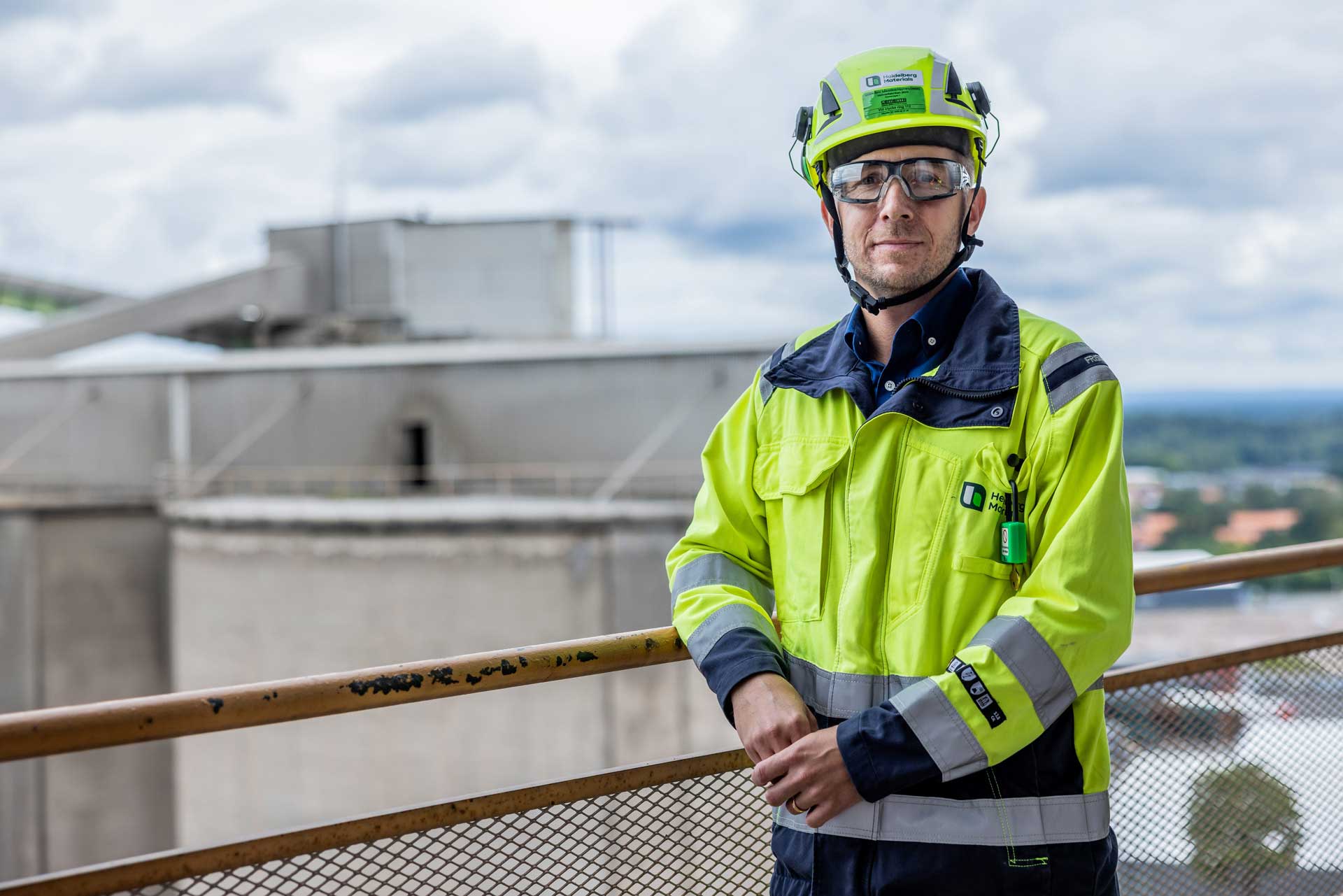
Employee Skövde.
Heidelberg Materials
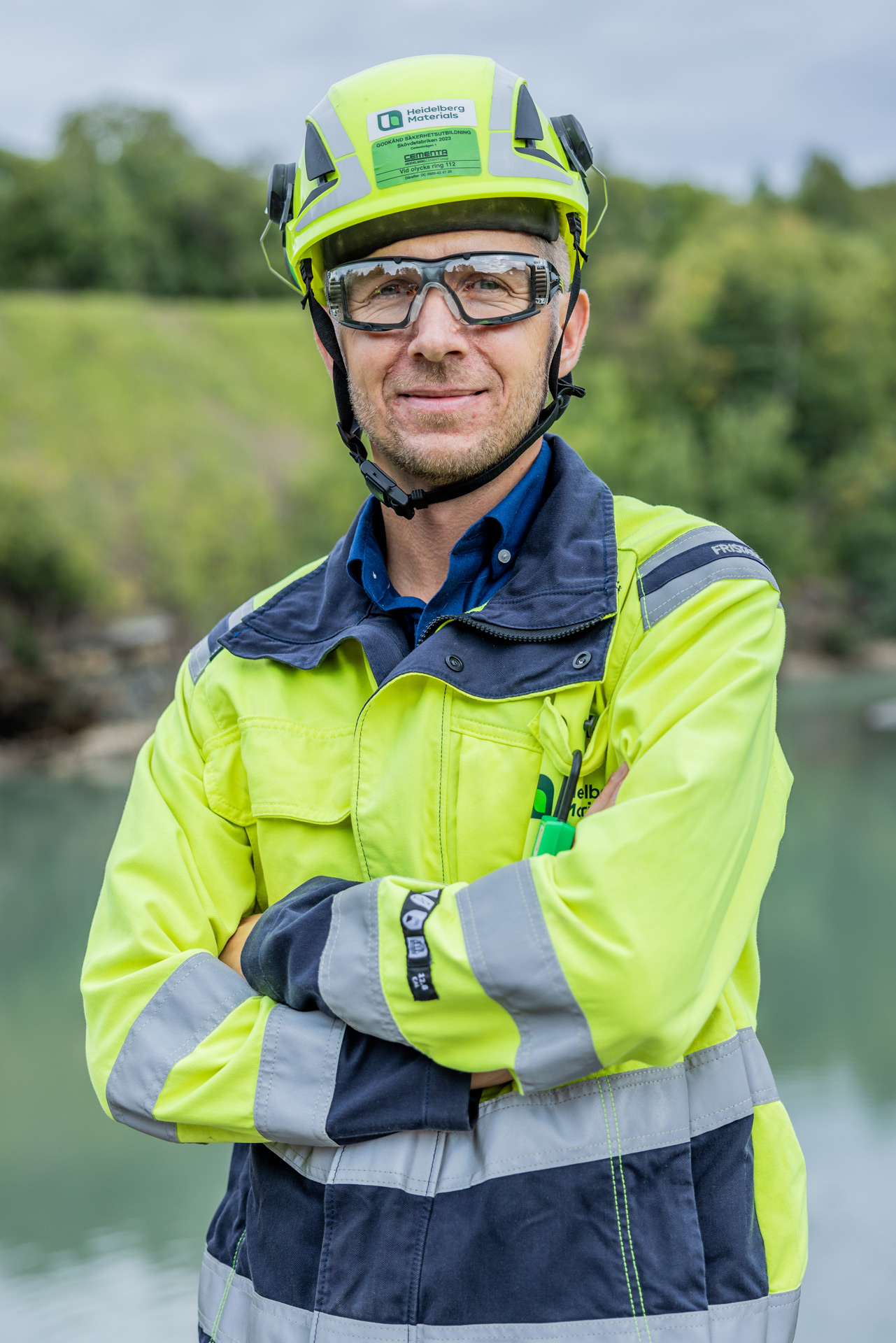
Employee Skövde.
Heidelberg Materials