Taking concrete recycling to the next level
Concrete is essential for building the infrastructure of the future. It forms the foundation of our roads, homes, offices and the cities we live in. The benefits are manifold: Concrete is durable, affordable, and produced locally. However, the production of cement, the “binder” in concrete, is CO₂-intensive.
To further reduce the climate and environmental impact of our products on our path to net-zero emissions by 2050, we are driving a broad range of different levers. However, the task is particularly complex. Two thirds of the overall CO₂ emissions are unavoidable due to the process of burning limestone at high temperature to produce clinker, a key ingredient of cement.
Innovating technologies on our path to net zero
A key driver to reduce the carbon footprint of our processes and products lies in developing scalable and cost-efficient technologies. We are currently piloting our proprietary ReConcrete approach on a larger scale, leveraging novel technologies to address multiple challenges at the same time:
- Recycling concrete completely through selective separation, enabling us to reuse 100% of products in concrete production
- Capturing and storing unavoidable CO₂ process emissions through enforced carbonation
In this article, we will explore ReConcrete’s advantages and its potential to close the material loop while actively reducing the amount of CO₂ that is released into the atmosphere.
The limits of conventional recycling
Concrete mainly consists of a mixture of cement, water, and aggregates (e.g. sand and gravel). At the end of a building’s service life, concrete can be recovered and further processed. Conventional recycling involves separating concrete from other construction and demolition waste, followed by further crushing and sieving to separate coarse and fine fractions. However, a substantial amount of cement stone still sticks to the sand and gravel.
If this unwanted constituent were to be reused in fresh concrete, it would absorb a substantial amount of water, requiring more cement and additives which affects the overall quality. In addition, the cement stone would also reduce the aggregates’ strength. Similarly, the fine fractions of the recovered materials also add little to no value as a recycled material.
As a result, old concrete is usually crushed without sieving. The resulting granulate is used for road base construction or earthworks. While still better than landfilling, it does not leverage the original quality of the material for fresh concrete or cement production, effectively leaving significant CO₂-saving potential untapped.
The delicate art of recycling concrete
Our R&D scientists set out to find innovative approaches and suitable equipment to effectively remove the cement stone from sand and gravel. They found a solution in a processing method that leverages shear force applying significantly lower pressure to free the surface of the sand and gravel grains from the cement stone.
Together with an equipment supplier, they further developed a suitable process and optimised machinery to introduce a potential game changer for recycling concrete and cement. By adapting the equipment to the needs of our industry, sand with properties nearly equivalent to natural materials can be recovered. This paved the way to reprocess large amounts of sand into concrete.
For the coarser fraction, the gravel, our process yielded even better results – with potential replacement rates of up to 100 percent without impairing the quality. After first successful trials, our scientists knew they had reached an important milestone on the path to closing the material cycle for sand and gravel.
Ramping up selective separation
In July 2024, we opened a first-of-its-kind recycling facility for selective separation near Katowice, Poland. This enabled us to introduce and test the new recycling technology at industrial scale. By achieving a more sophisticated separation and sorting of demolition material, we are now able to fully recycle concrete without quality loss and substitute virgin materials in concrete production to maximal extent.
While sand and gravel can now replace its virgin counterparts, what happens to the cement stone? Unlike the conventional method of simply crushing concrete, selective separation efficiently decomposes old concrete into all its original constituents: In addition to high-quality gravel and sand, we also recover the cement stone in the form of fine powder called recycled concrete paste (RCP). Thanks to the attrition-driven soft grinding process, the cement stone is cracked and rubbed off from the surfaces of gravel and sand. The process is fully mechanical and fully dried, resulting in favorable costs and ease of implementation.
Unlocking new ways of reducing CO₂
Traditionally viewed as a “contaminant“ sticking to recycled aggregates, the now separately recovered RCP offers significant decarbonisation potential in several ways.
Since RCP is already finely ground, it can be simply added to the raw material mix during concrete production, partially replacing limestone and saving process CO₂ emissions. For a typical industrial RCP from a normally carbonated concrete structure, about 150 kg CO₂ per tonne of RCP can be prevented from being emitted.
Even more interestingly, the recovered RCP proved to be valuable beyond its use of replacing virgin materials. Through a process called enforced carbonation, additional CO₂ savings can be unlocked. To explore this technology outside of the lab environment, we are currently building an industrial demonstrator facility for enforced carbonation at our cement plant in Górażdże, Poland. The RCP obtained through selective separation at the nearby recycling plant will soon be transported to the demonstrator facility in Górażdże.
Enforced carbonation in a nutshell
The cement stone naturally binds CO₂. As a result, concrete acts as a CO₂ sink over its lifecycle and helps compensate for 20 percent of the emissions caused during its production. In concrete structures, this process is intentionally slow to prevent corrosion of steel reinforcement.
With enforced carbonation, we take advantage of this basic characteristic and accelerate it. Instead of letting the RCP naturally carbonate in the ambient air, we expose the powder to our own kiln gases from cement production, which contain about 20 percent CO₂. This enables us to achieve carbonation much faster. Lab and industrial trials have shown that practically complete carbonation can be achieved in less than half an hour.
The carbonation reaction is spontaneous and requires no external energy inputs. This makes it a very efficient carbon capture and storage (CCS) technology compared to other alternatives. In our industry, CCS is being increasingly tested and applied as a means to prevent unavoidable CO₂ process emissions from being released into the atmosphere.
There are even more uses to RCP. After its carbonation, it becomes a reactive material which can be applied to replace clinker in composite cements as a supplementary cementitious material (SCM). Another 750–850 kg CO₂ per tonne of RCP can be avoided in this way. Overall, with the CO₂ binding on the one hand and the clinker substitute on the other, enforced carbonation has the potential of saving of one ton of CO₂ per tonne of RCP.
Looking ahead
We are now entering a crucial phase, in which our pilot projects focus on validating our ReConcrete approach on an industrial and commercial scale. With a capacity of up to 100 tonnes of concrete per hour, we are the first company in the industry to introduce high-quality, selective concrete separation at this scale. The nearing completion of our industrial pilot facility for enforced carbonation will mark yet another important milestone for ReConcrete, which in 2022 has earned us the German Innovation Award for Climate and Environment.
Already back then, the jury was impressed by the massive potential to significantly reduce CO₂ emissions and promote circularity in construction. It is now up to us to verify and realise this potential out in the field in Poland and beyond. Only if large volumes of waste concrete are processed in a very cost-efficient manner across different regions, the market‘s needs can be addressed properly resulting in widespread acceptance and adoption of full-fledged recycling and circular concrete production within our industry.
Downloads
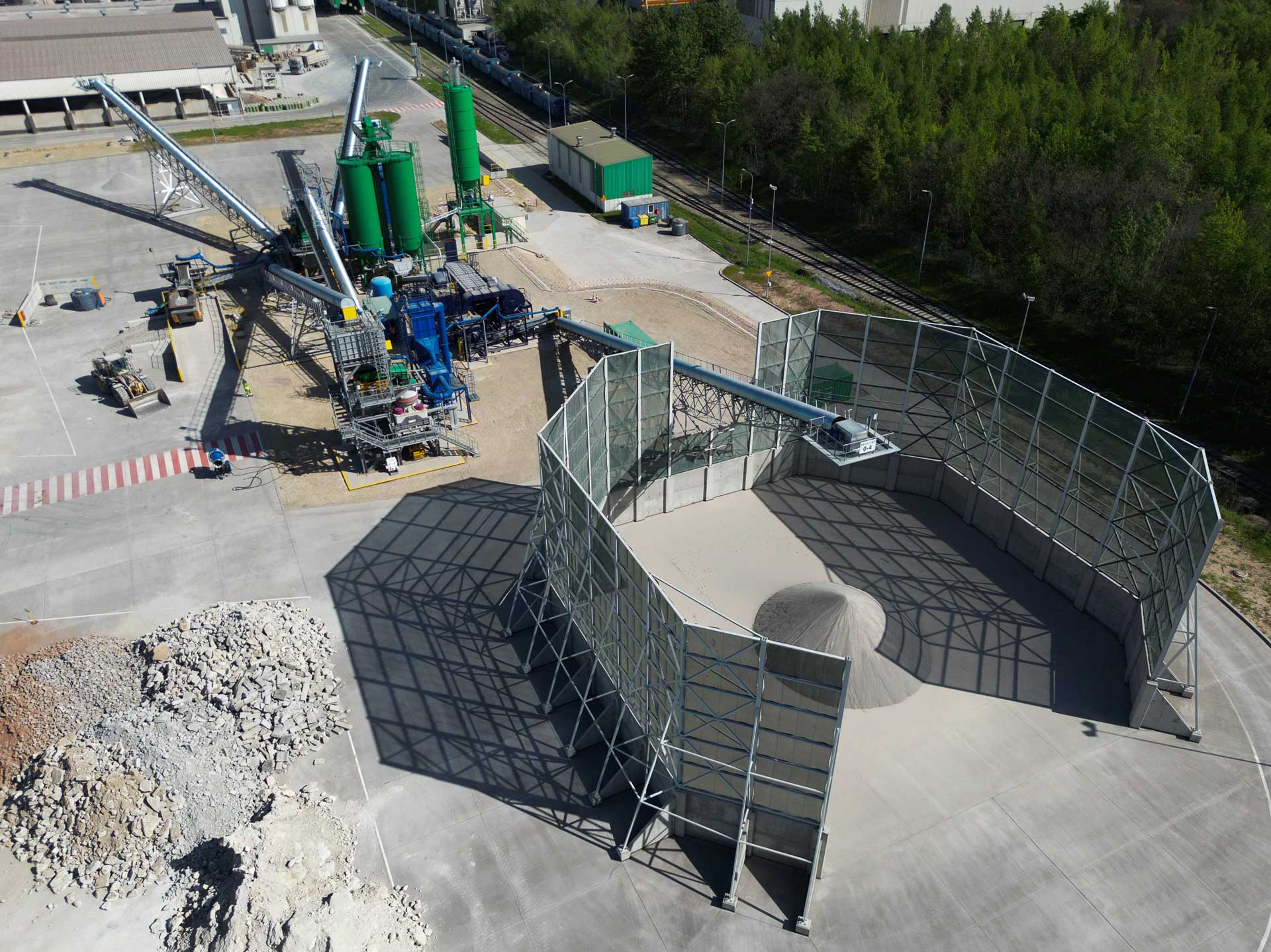
Recycling facility Katowice (2). Recycling facility at Heidelberg Materials’ production site near Katowice, Poland
Heidelberg Materials
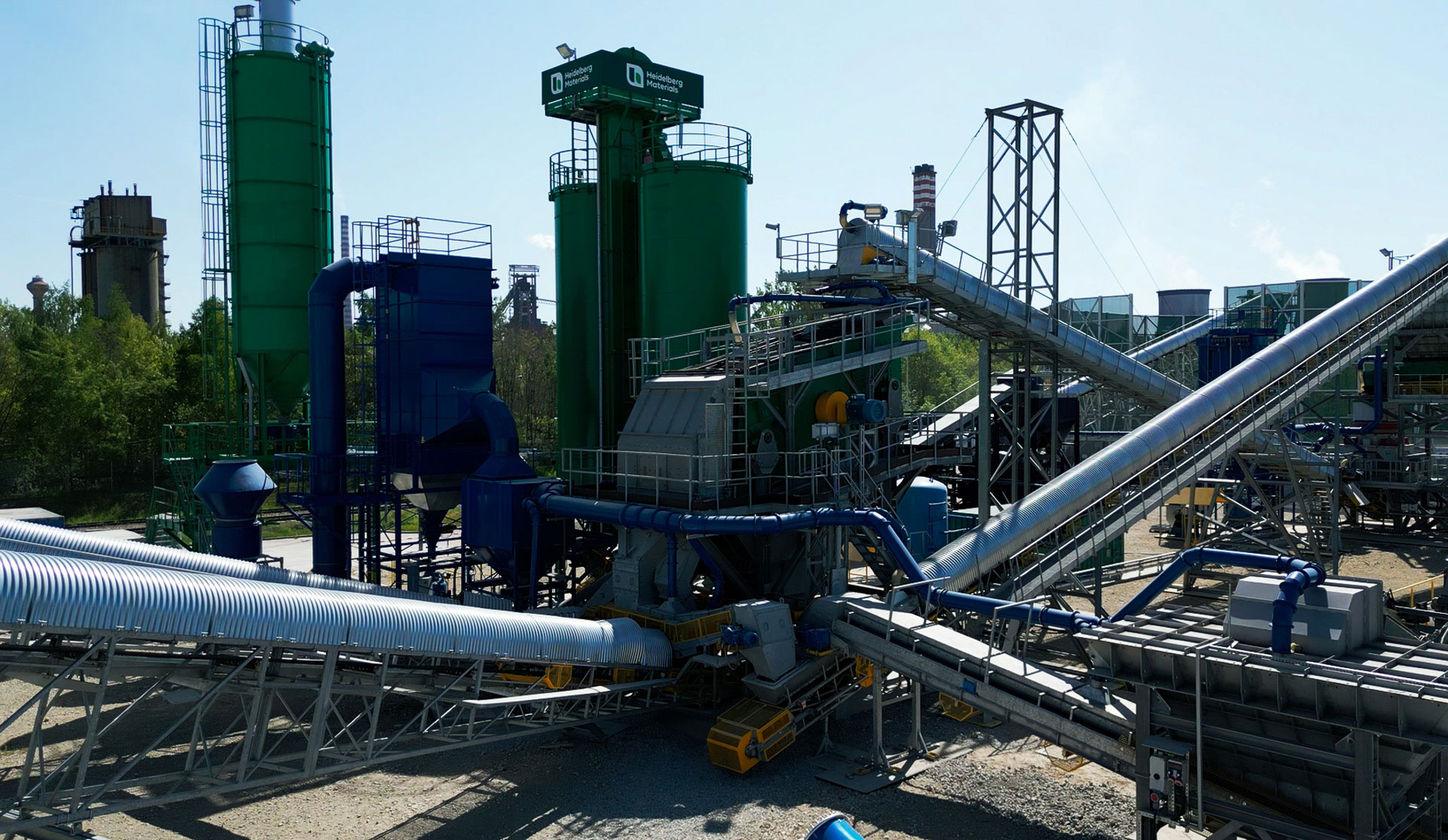
Recycling facility Katowice (1). Recycling facility at Heidelberg Materials’ production site near Katowice, Poland
Heidelberg Materials
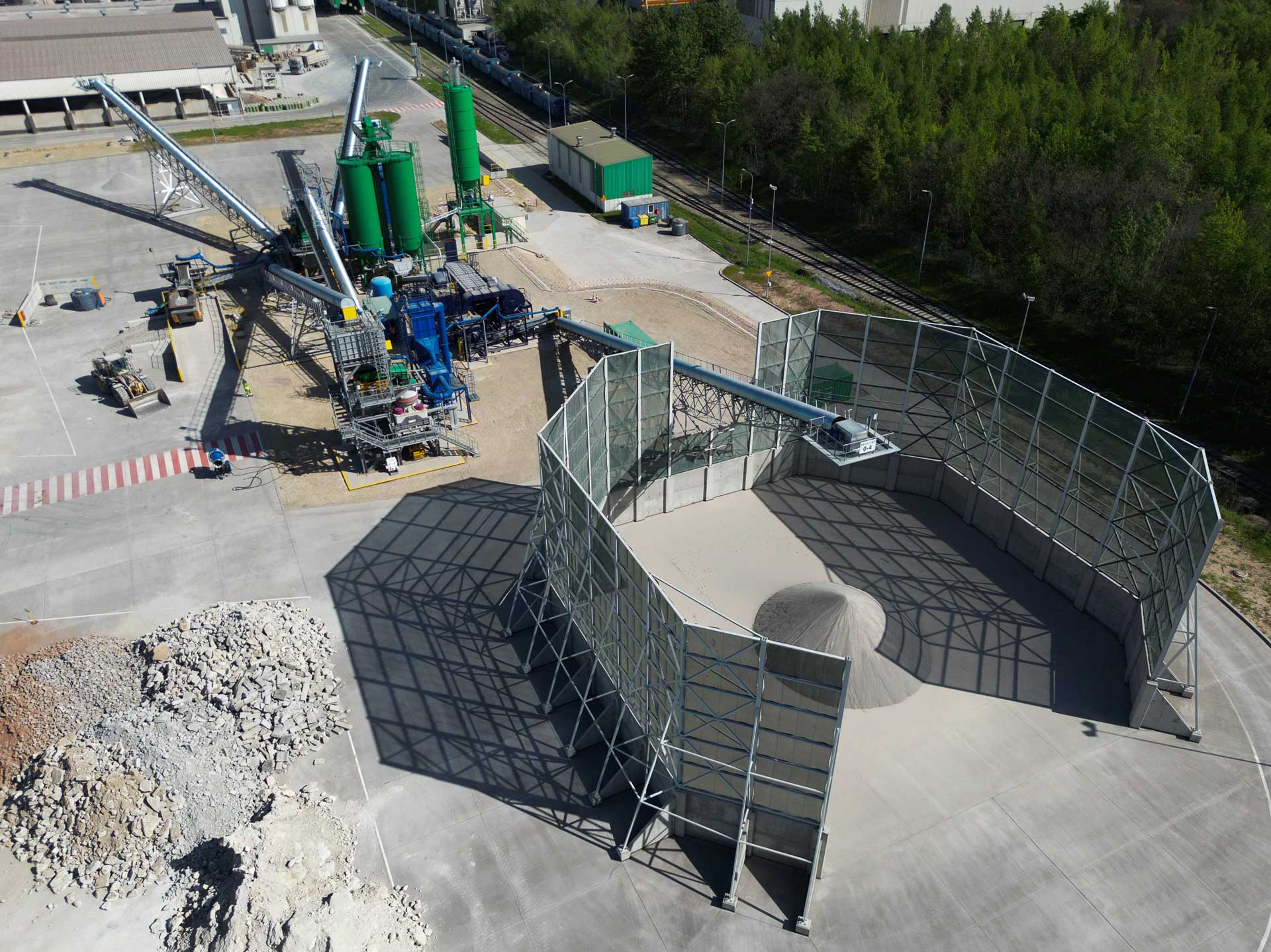
Recycling facility Katowice (2). Recycling facility at Heidelberg Materials’ production site near Katowice, Poland
Heidelberg Materials
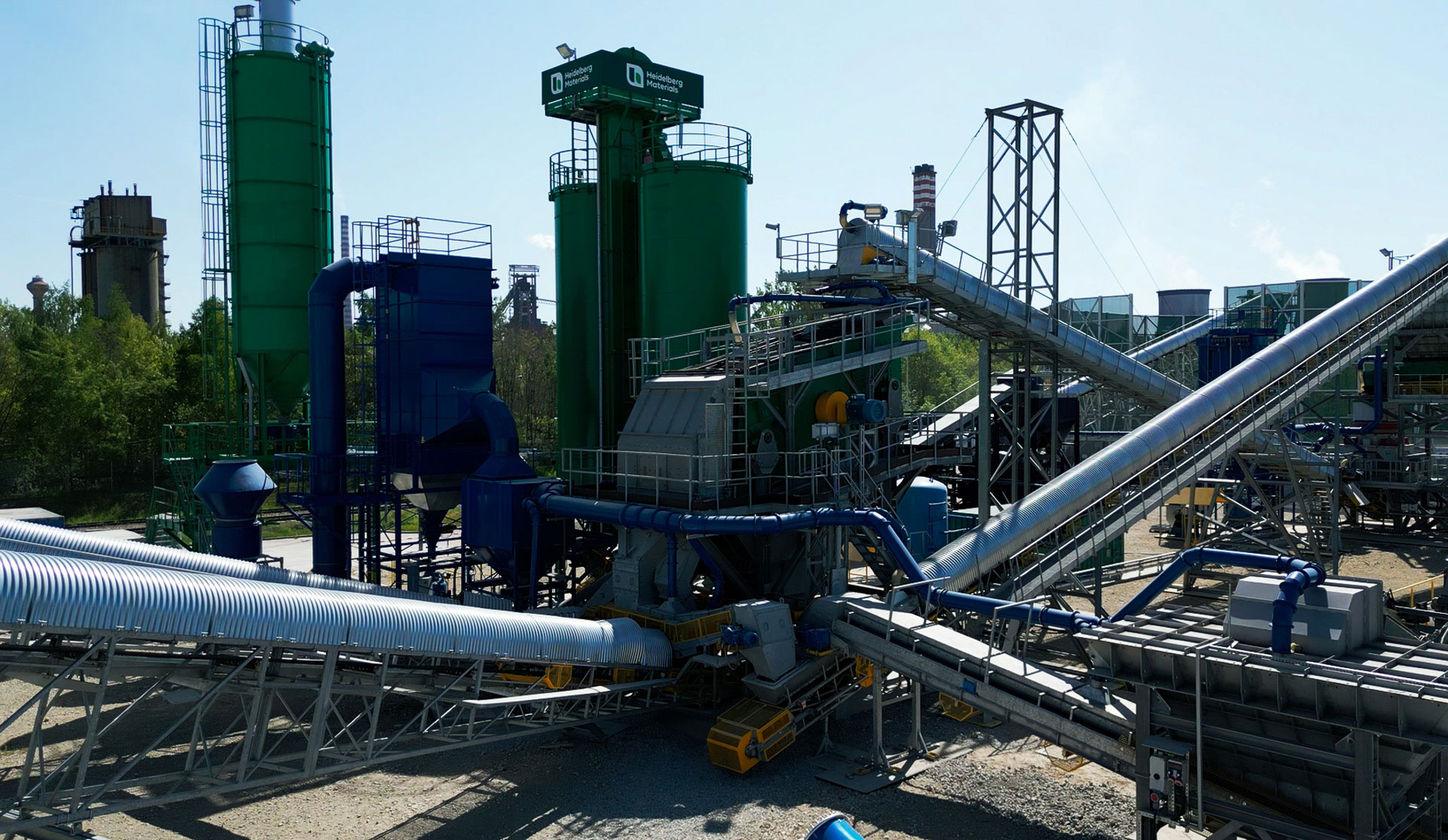
Recycling facility Katowice (1). Recycling facility at Heidelberg Materials’ production site near Katowice, Poland
Heidelberg Materials