Occupational health and safety
Always close to where the action is
People who come to one of our plants for the first time are often overwhelmed by the multitude of activity. There are heavy machines operating in the quarry, whose wheels alone are twice your height; the rotary kiln, in which limestone is burned at over 1000 degrees Celsius, causing you break out in a sweat even from a safe distance; the mixing plants, with so many cubic metres of concrete being mixed that no bakery in the world could compare; and, amidst of all this, our fleet of green trucks that deliver our products to their final destinations. It gets clear very quickly: Here is a lot of action taking place!
And this is where occupational health and safety comes into play: “To make an omelette, you have to break a few eggs”, as the saying goes – but, in this case, that is exactly what must be avoided. Our overarching goal is to ensure that no one is ever injured or harmed at work, through work or due to our business activities.
Working without safety precautions is like playing Russian roulette
This is true at work and even at home. Simply recalling your last trip on the motorway is enough to drive this point home – hazards can arise anywhere. These hazards must be eliminated, i.e. it must be ensured that they do not occur in the first place. If this is not possible, they must be mitigated to the greatest-possible extent so that they do not lead to injury or damage. Back to the image of Russian roulette: Our aim is to remove the bullet from the revolver’s drum before it goes off.
This places great emphasis on prevention – taking action before something happens. To do this, we need to know where the “bullet” is and how to remove it effectively. In order to successfully do so, we carry out risk assessments and investigate and analyse accidents, incidents and unsafe situations, for example.
And these are probably the first aspects that would have occurred to me regarding the field Occupational Health & Safety before I joined the department. As a psychologist, I was familiar with the topic of risk assessment from my studies, especially with regard to psychological hazards and mental health. Reporting and investigating accidents is not a far cry from that. Otherwise, my experience with the topic derived mainly from the occasional training workshop, a practical driving safety training, an ergonomic workplace consultation I had taken part in – i.e. pretty standard and everyday topics for office personnel.
But from day one at Heidelberg Materials, there has always been another aspect present as well: on my first day I received a set of personal protective equipment in addition to my laptop and mobile phone. I proudly displayed my new safety helmet in my office. Thus, it reminded me constantly of the great diversity and many different jobs that Heidelberg Materials offers.
Admittedly, at the time, my helmet served mostly a decorative function. I rarely got the opportunity to use it for its intended purpose. But I seized every opportunity to visit our production sites and was always happy to use it where it was meant to be used – outside, on site. Time and again, these visits provided fascinating insights into a completely different world compared to my office routine.
Occupational health and safety: many jobs in one
This is why, when the opportunity arose to join the safety department, I did not hesitate for a moment. And, here, I’ve found a job that offers the versatility I had hoped for – and much more.
My first project was to introduce "safety conversations” as an instrument of visible felt leadership throughout Germany, including a reporting tool. This meant adapting the Group's template for Germany, developing a holistic training concept and then training all managers and supervisors all across Germany on this concept together with my colleagues.
Modern workplace safety – it's all about people
In recent years, experts in occupational health and safety have recognised that, although laws, standards, regulations etc. provide the necessary foundation, it is ultimately down to the people. People make the decisions and take the actions, which is why the area of behaviour-based safety has moved into focus. Thus, tools such as the safety conversations are of great importance in helping to raise awareness of workplace safety issues so that people can make the best-possible decisions in the interests of safety, even in unexpected situations and under stress.
This first project showed me that occupational safety is a very diverse field that interfaces with all business areas and functions and offers a stimulating work environment for people with or without a technical background. Moreover, even if the content is the same, no two training workshops are the same. The character of each training session is a product of the questions, discussion points and views of the participants. This means that I as the trainer also take new ideas with me and learn more every time. There is probably no other area of the business that would have enabled me to get to know so many different colleagues so quickly – and to get to see more of Germany as an added bonus. After the training sessions, my colleagues on site often gave me insider tips on places of interest, beautiful places to go running or good restaurants.
After all, the measures, actions and projects are ultimately aimed at protecting the health and safety of all of us. It is better to hear one more opinion in advance, to integrate one more perspective and to convince one more sceptic, who then stands behind the change and supports its implementation.
COVID-19. Protecting physical and mental health
Unforeseen events outside the company also ensure that things remain challenging and varied, most recently the COVID-19 pandemic. The Occupational Health & Safety functions at Heidelberg Materials play a central role in crisis management. We support the sites in the development and implementation of protective measures and respond to current needs and requirements, such as pandemic-related occupational safety standards issued by the government. In the current situation, it is also a personal matter of concern to me that, in addition to physical health, which is being protected by many measures, mental health is not forgotten.
Another aspect I still love about my job is the many different people I get to work with. Two highlights from the last few months are particularly memorable: the first was an international occupational safety meeting in London with colleagues from Western and Southern Europe. During my studies abroad in the UK, I would never have dreamed of taking a behind-the-scenes tour of a construction site right in the City of London together with colleagues from seven countries before visiting the Tower of London in full protective gear!
One day on a concrete pump: simply amazing
The second highlight is the day I spent alongside a colleague operating a concrete pump. While preparing for a safety workshop, I realised that I knew next to nothing about the daily routine of these colleagues and what the job actually entails. The experience was amazing – I wouldn't have imagined how many things you need to know and do to ensure a good and safe job. Not only do you have to know the machine and our product very well, there are also high demands on physical fitness and the ability to handle conflicts – and language skills in at least one foreign language are certainly also a plus to get along on the construction site.
I have now been to many of our production sites and become much more familiar with the places that impressed me so much at the beginning. But, every now and then, I still take the opportunity to climb up to the highest point of a plant and look out at the vibrant activity taking place below. This is a great way to gain new perspectives and ideas, just like the ones I receive from the training sessions. It's worth the climb!
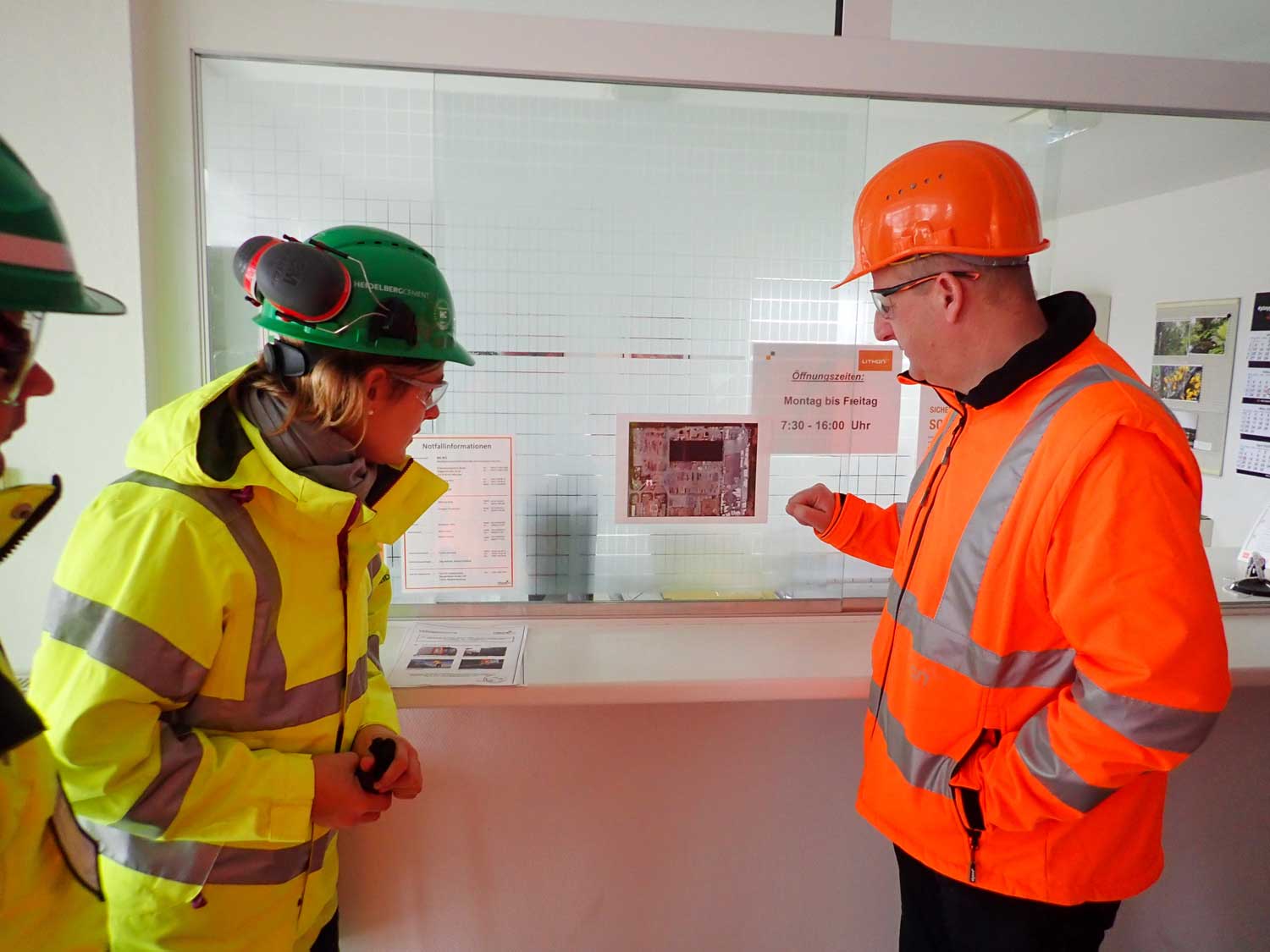
Plant visit at LithonPlus.

Plant tour from above.
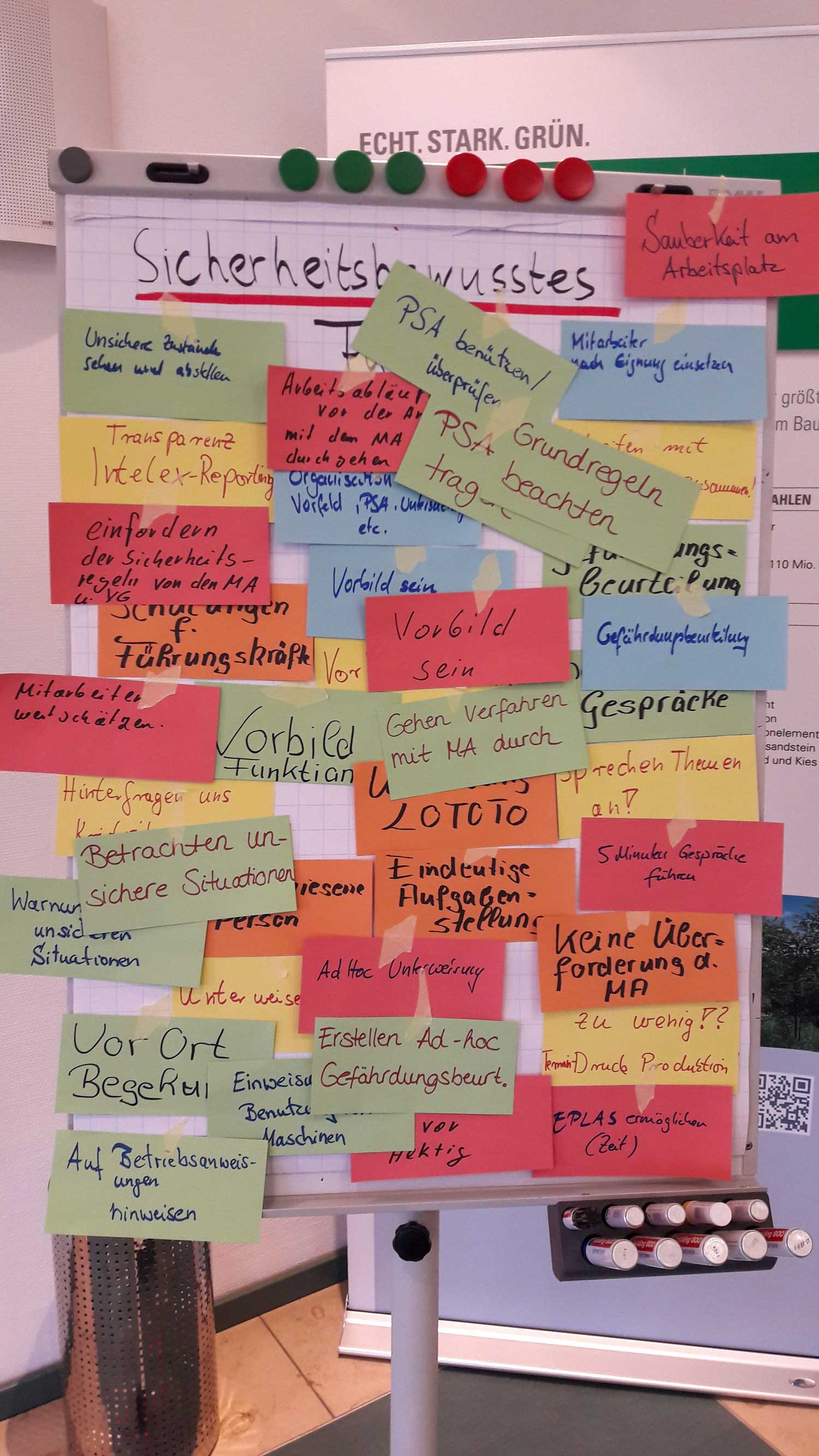
Input from a training session.

In the truck.

Katharina Fischer London Plant.
Heidelberg Materials
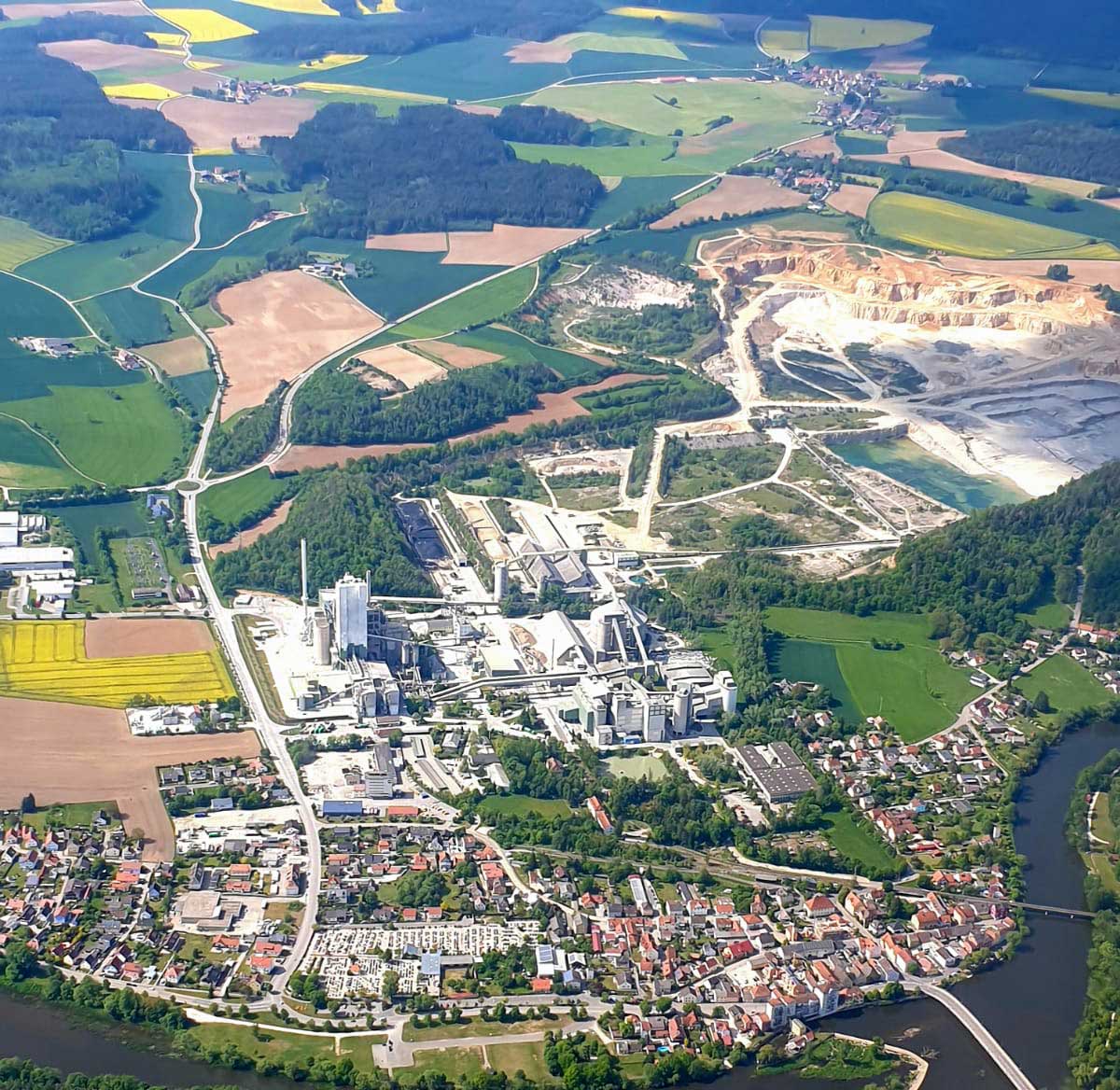
Plant from the air.
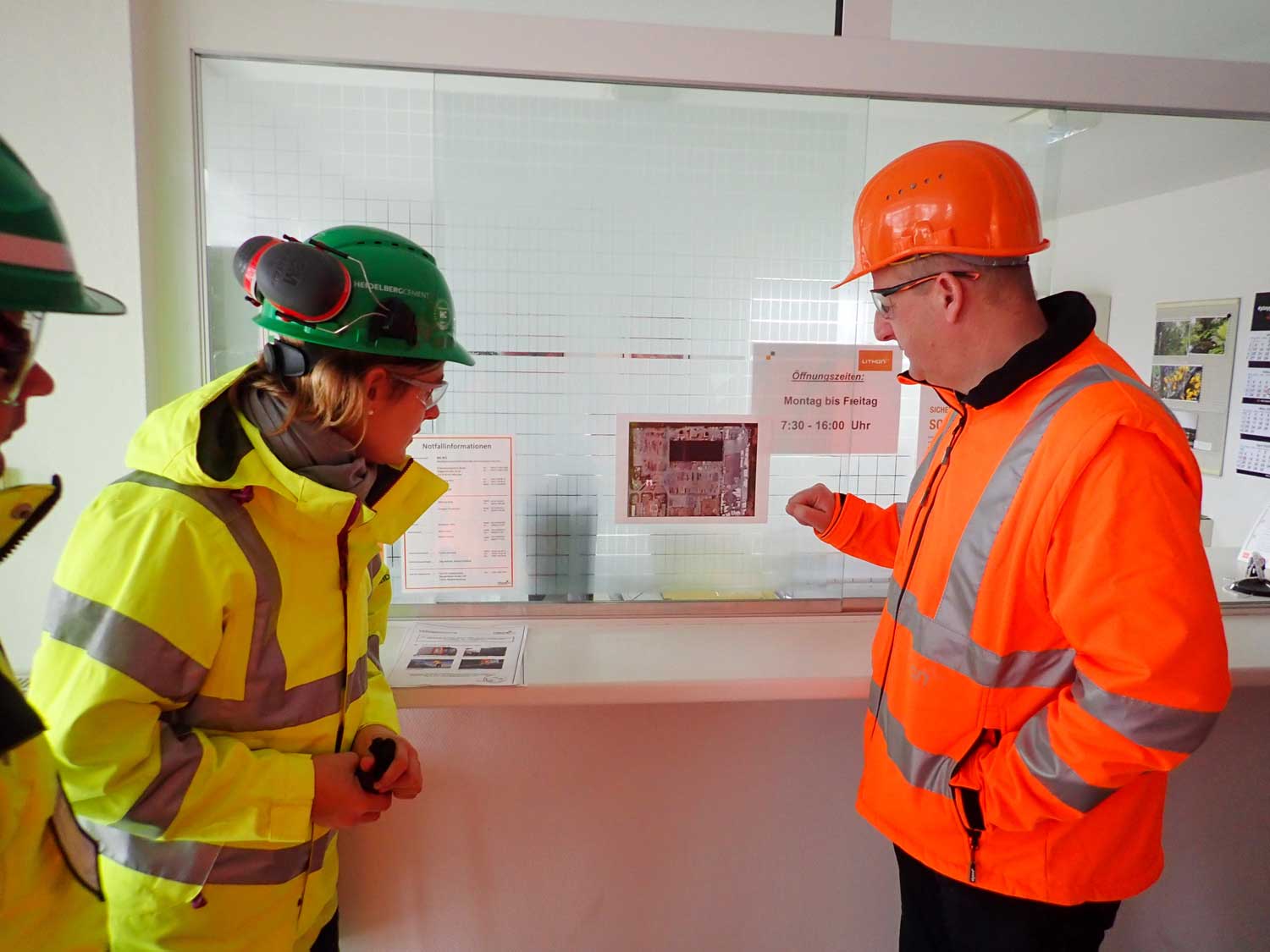
Plant visit at LithonPlus.

Plant tour from above.
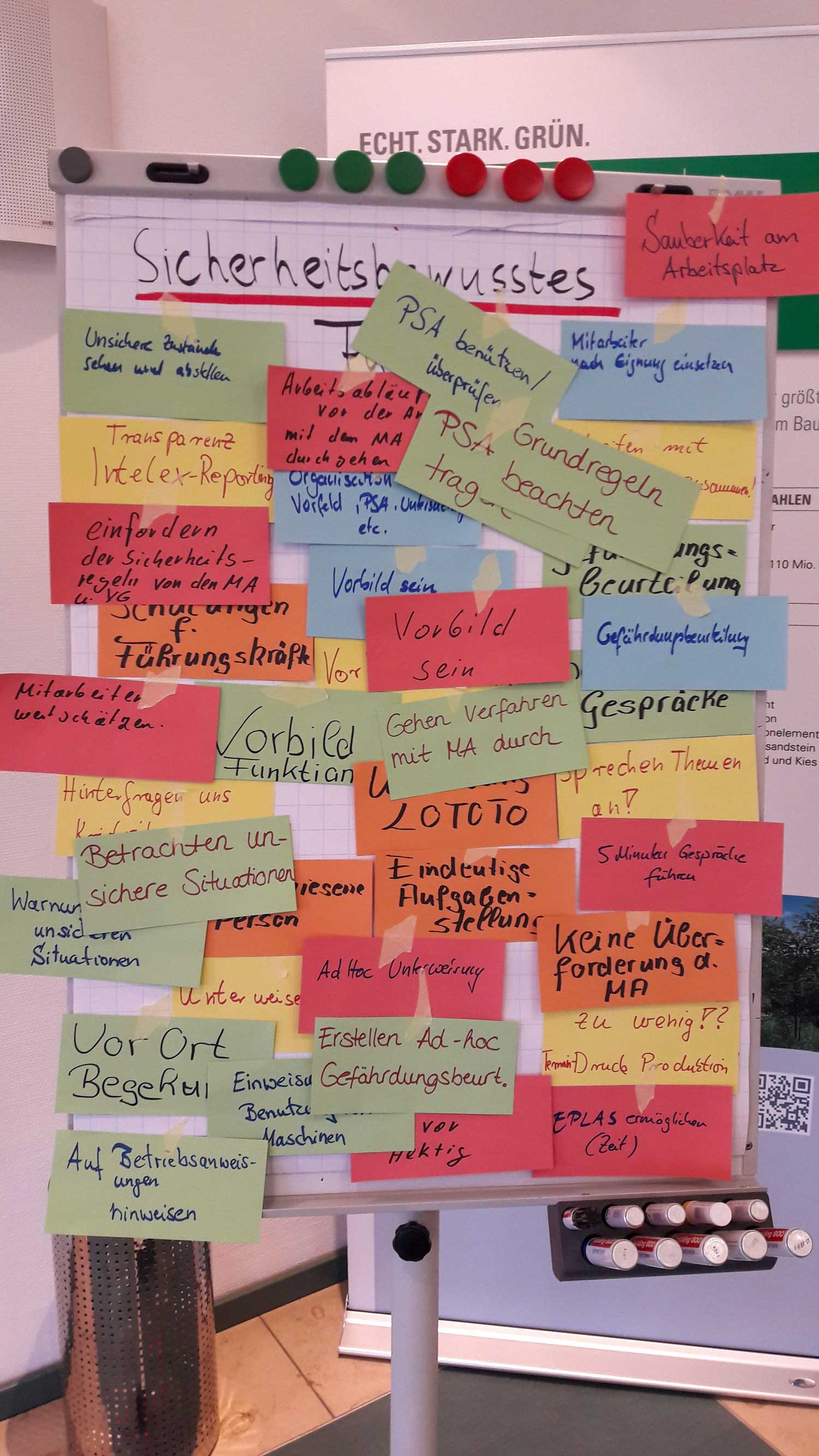
Input from a training session.

In the truck.

Katharina Fischer London Plant.
Heidelberg Materials
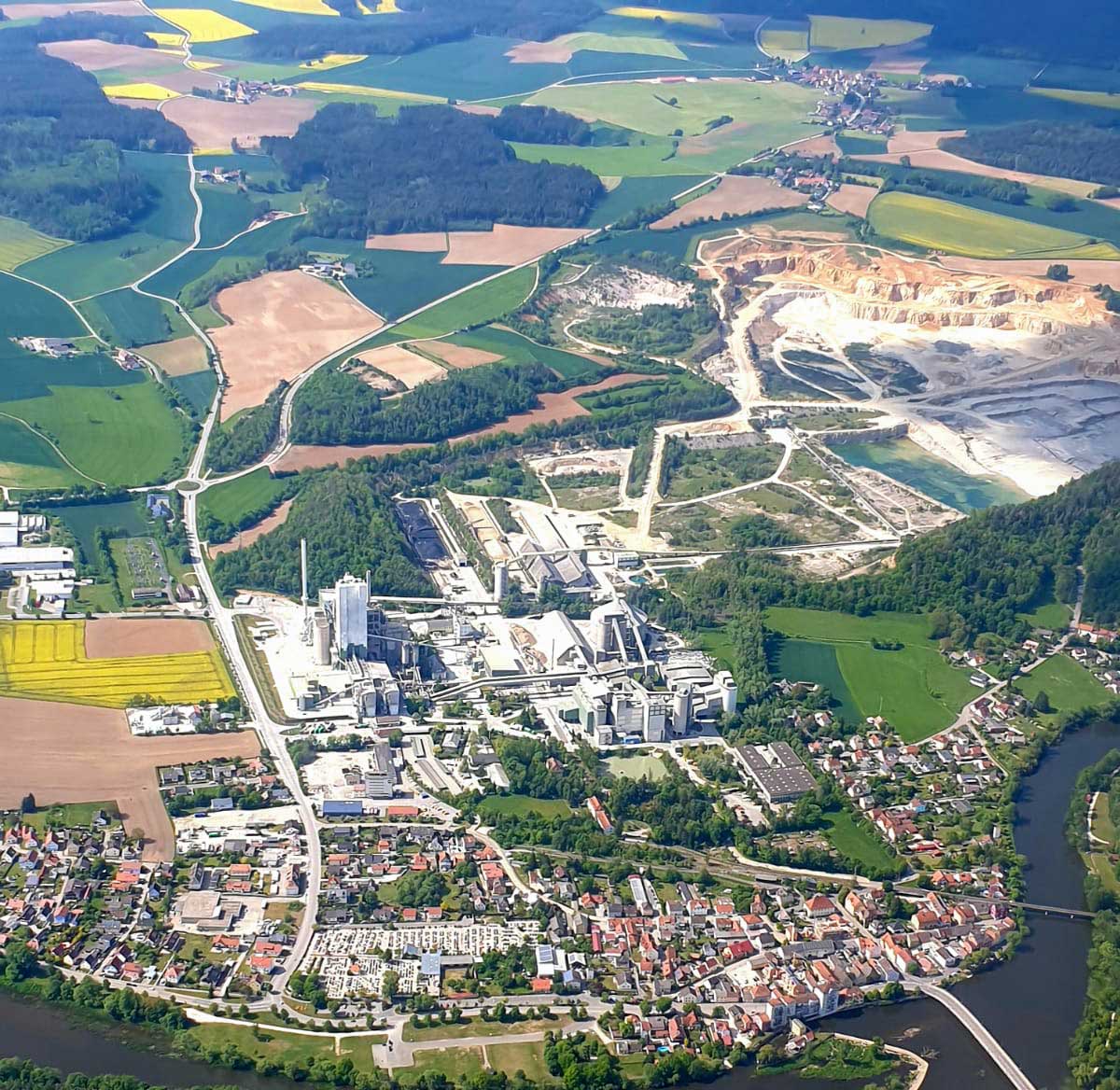
Plant from the air.